Rubber diaphragm fabric Selection Guide
The adhesion between various fabrics and rubbers (including the fabric’s adhesion to the original rubber, its adhesion after primer application, and comparisons across different fabric–rubber pairings); the three major fabric types—nylon, polyester and aramid (Nomex); the effects of surface treatments and fabric density on adhesion; and, finally, the comparative strength, temperature resistance and solvent resistance of each fabric type. By exploring mechanical interlocking, physical adsorption and chemical coupling mechanisms—along with common surface‑modification treatments such as RFL dipping and isocyanate priming—this article provides guidance for choosing and optimizing fabric reinforcements to ensure reliable diaphragm performance under high pressure, dynamic loads and extreme environments.
1. Fabric–Rubber Adhesion
1.1 Adhesion Components
Total adhesion force arises from three mechanisms:
-
Mechanical interlocking, due to fiber hairs and fabric weave engaging the rubber;
-
Physical adsorption, including van der Waals forces, dipole interactions and hydrogen bonding;
-
Chemical coupling, via covalent bonds or coupling agents between fabric and rubber.
1.2 Untreated Fabric Adhesion
Unmodified fabrics—lacking active groups for sulfur cross‑linking—exhibit relatively low adhesion. Synthetic fibers like polyester and aramid are especially inert, yielding pull‑off strengths only around 20–30% of the rubber’s own breaking strength when left uncoated.
1.3 Primer and RFL‑Dipped Adhesion
Treating the fabric with resorcinol–formaldehyde–latex (RFL) or polyisocyanate primers deposits a semi‑crosslinked interlayer that co‑vulcanizes with the rubber, boosting adhesion by 2–3×. Polyisocyanate pretreatment further introduces reactive groups to enhance chemical coupling.
1.4 Fabric–Rubber Pairings
-
Nylon – NBR: Nitrile rubber coated onto nylon can achieve peel strengths of 3–50 N/cm², depending on dip formulation and conditions.
-
Polyester – EPDM: Untreated polyester relies mainly on mechanical grip and shows low adhesion; RFL treatment can raise lap shear strengths to 1.5–2.0 MPa.
-
Aramid (Nomex) – Sulfur/Peroxide Vulcanization: Untreated aramid has interfacial shear below 0.5 MPa; surface activation and RFL or isocyanate‑enhanced dips can boost this to 1.0–1.2 MPa.
2. Fabric Types: Nylon, Polyester and Aramid
2.1 Mechanical Properties
-
Tensile Strength (dry): Aramid > Polyester ≈ Nylon.
-
Modulus: Aramid exhibits very high stiffness (E-modulus > 50 GPa) with low elongation (3.7–4.2%); nylon and polyester have lower moduli and higher elongations.
2.2 Temperature Resistance
-
Polyester: continuous use up to ~120 °C;
-
Nylon‑6/66: up to ~80 °C but prone to thermal shrinkage;
-
Aramid (Nomex/Kevlar): stable above 500 °C with inherent flame resistance.
2.3 Solvent Resistance
-
Nylon: good resistance to oils and weak acids/bases; vulnerable to strong acid attack;
-
Polyester: resistant to most organic solvents but subject to alkaline hydrolysis;
-
Aramid: outstanding chemical resistance to solvents and oils; degraded by strong acids or alkalis only.
3. Surface Treatments to Enhance Adhesion
3.1 Surface Activation
Plasma, oxidative or chemical treatments introduce polar groups on inert fibers (especially aramid), increasing adhesion—but may reduce tensile strength by ~5–10%.
3.2 RFL Dipping
RFL (resorcinol–formaldehyde–latex) systems coat fibers with a resin–latex blend that co‑vulcanizes with rubber, routinely raising lap shear strengths to 2–3 MPa versus sub‑1 MPa for untreated fabric.
4. Fabric Density vs. Adhesion
4.1 Mechanical Interlock
Lower to moderate fabric density (e.g. ~32 ends/cm × 27 picks/cm) allows deeper rubber penetration and better mechanical grip.
4.2 Over‑Density Drawbacks
Excessive density yields thin interfacial rubber layers, stress concentrations and reduced peel strength.
5. Comparative Performance Summary
Fabric Type | Tensile Strength | Service Temperature | Solvent Resistance |
---|---|---|---|
Nylon‑6/66 | 600–800 MPa | < 170 °C | Oils, weak acids/bases |
Polyester | 800–900 MPa | < 150 °C | Most organics (alkaline hydrolysis) |
Aramid (Nomex/Kevlar) | 2,600–2,900 MPa | < 250 °C | Excellent (resists solvents/oils) |
Conclusion
-
Adhesion relies on mechanical, physical and chemical contributions—all must be optimized.
-
Surface treatments (RFL dipping, isocyanate primers) are essential to achieve high fabric–rubber bonding.
-
Material selection balances strength, temperature and chemical resistance: nylon for moderate conditions, polyester for higher heat/chemical environments, and aramid for extreme heat, high strength and flame resistance.
-
Fabric density should be tuned to permit adequate rubber wetting while avoiding stress‐concentrating thin interlayers.
By applying these principles, engineers can choose and process reinforcement fabrics to ensure durable, high‐performance rubber diaphragms under demanding service conditions.
GENERAL SEALTECH offers a variety of fabric options for different application scenarios. You can choose by yourself or have our professional engineers recommend the appropriate fabric based on the operating conditions of the diaphragm.
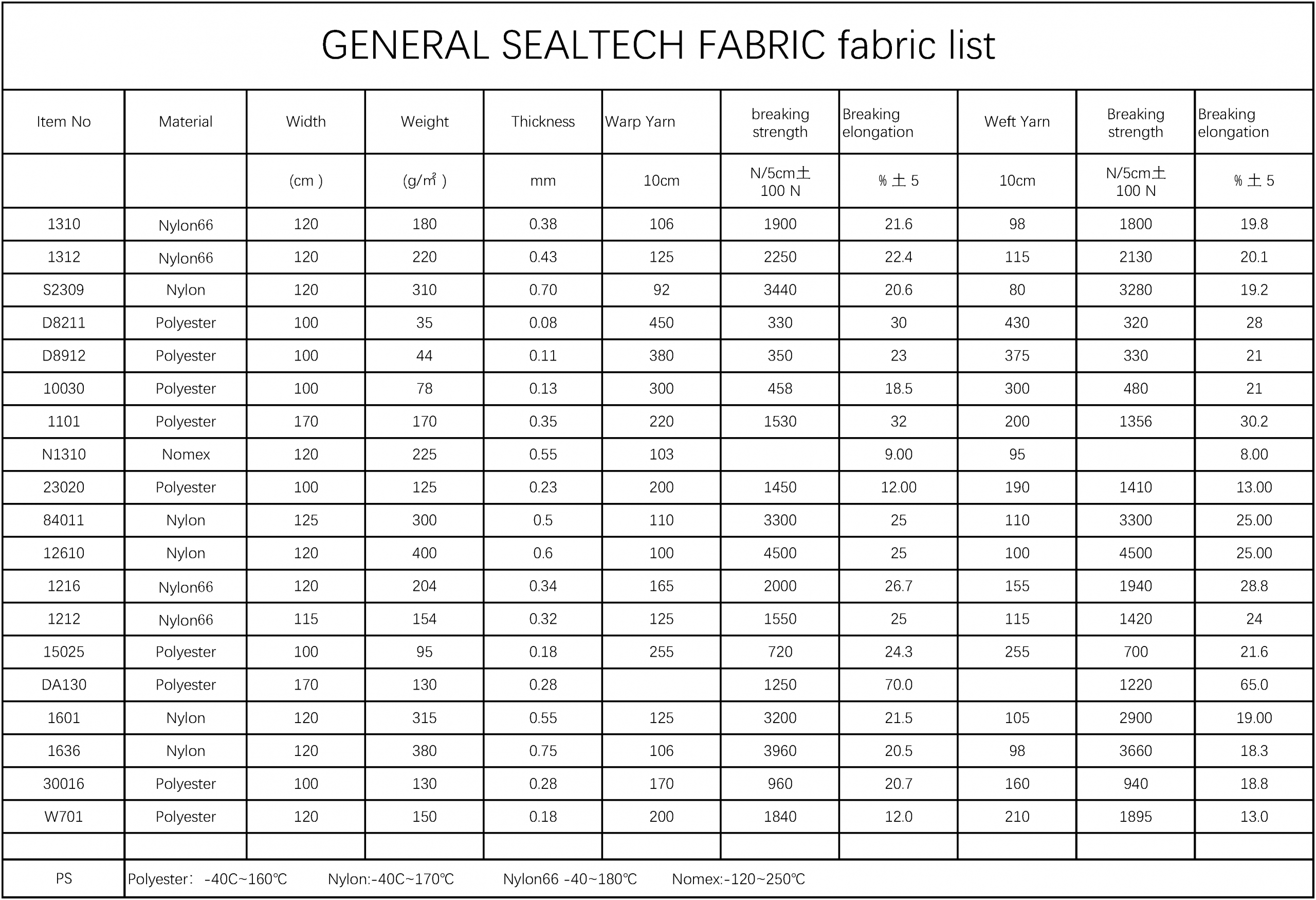
GENERAL SEALTECH RUBBER DIAPHRAGM FABRIC LIST