A diaphragm is a flexible barrier that separates two components and maintains their relative positions. It can be made from various materials such as rubber, fabric, or metal. The two most common types of diaphragms are the rubber diaphragm and the rolling diaphragm, which differ in their design and applications.
Rubber Diaphragm:
Rubber diaphragms are thin, flexible membranes made from rubber material. They are typically made from natural rubber, synthetic rubber, or silicone rubber. The rubber material gives these diaphragms high elasticity and durability, making them suitable for a variety of applications. This type of diaphragm is commonly used in industries such as automotive, pharmaceutical, and aerospace.
Design:
Rubber diaphragms have a simple yet effective design. They consist of a rubber sheet, usually circular in shape, that is stretched over a rigid frame. This frame can be made from metal, plastic, or any other material that provides support to the diaphragm. The edge of the diaphragm is held in place by the frame, and it is sealed to prevent any leakage between the two components it separates.
Applications:
Rubber diaphragms are commonly used in applications that require a flexible and durable barrier. One of its main applications is in control valves, where the diaphragm acts as a seal between the valve body and the control chamber. It allows the control of the flow of fluids or gases by moving in response to pressure changes. Rubber diaphragms are also used in pumps, where they act as a membrane to create movement and displacement of fluids. Additionally, these diaphragms are used as seals in pressure sensors, regulators, and actuators in various industrial machines.
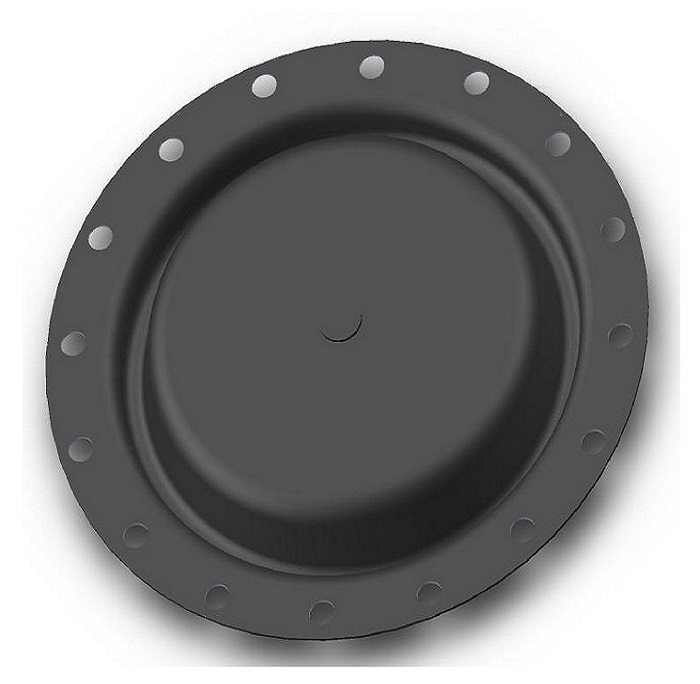
rubber diaphragm Regulator
Advantages:
Rubber diaphragms offer several advantages over other types of diaphragms. Due to their high elasticity, they can undergo repeated flexing without cracking or losing their shape. They are also resistant to corrosion, temperature changes, and chemical reactions, making them suitable for use in harsh environments. Moreover, rubber diaphragms are highly flexible, allowing for easy installation in different shapes and sizes.
Disadvantages:
While rubber diaphragms have many advantages, they come with some limitations as well. They are not suitable for high-pressure applications as they may deform or swell under excessive pressure, causing leakage. Rubber diaphragms also have limited compatibility with certain chemicals and fluids, which can cause them to degrade over time. They also have a limited lifespan as they can wear out or tear due to continuous use and exposure to harsh conditions.
Rolling Diaphragm:
Rolling diaphragms, also known as convoluted diaphragms, are a type of diaphragm with a corrugated or folded design. They consist of a cylindrical or conical-shaped rubber or plastic bellows that moves axially in response to pressure changes. These types of diaphragms are commonly used in industries such as automotive, aerospace, and medical.
Design:
Rolling diaphragms have a more complex design compared to rubber diaphragms. The bellows design allows for a larger range of motion, making them suitable for applications that require high stroke length. They are typically made from rubber or plastic material and are reinforced with fabric or metal layers to provide structural support.
Applications:
Rolling diaphragms have a wide range of applications. One of the most common uses is in automotive steering systems, where they act as a seal between the steering gear and the steering column. In this application, the rolling diaphragm provides smooth and precise movement while preventing any leakage. They are also used in pneumatic and hydraulic actuators, where they convert the pressure into mechanical movement. Additionally, rolling diaphragms are used in medical devices such as compressors, pumps, and valves.
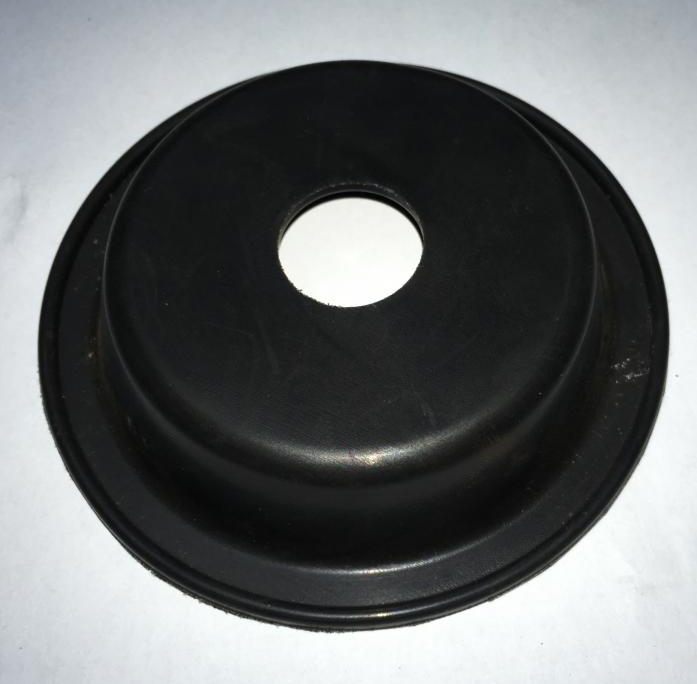
Rolling diaphragm piston servo diaphragm4
Advantages:
The unique design of rolling diaphragms offers several advantages. Due to the convoluted shape, they can move over a larger stroke length without losing their shape or compromising their performance. They can also withstand high pressures, making them suitable for use in hydraulic systems. Moreover, they have a longer lifespan compared to rubber diaphragms as they can withstand high flexing and pressure without tearing or cracking.
Disadvantages:
Despite their many advantages, rolling diaphragms also have some limitations. They are more complex and expensive to manufacture compared to rubber diaphragms. Due to their large range of motion, they are prone to fatigue and may eventually fail if subjected to continuous high-pressure cycles. Additionally, the bellows design makes them less flexible and more challenging to install in different shapes and sizes.
Comparison:
The following table summarizes the main differences between rubber diaphragms and rolling diaphragms:
Property | Rubber Diaphragm | Rolling Diaphragm |
Material | Rubber | Rubber or Plastic |
Design | Single, flat sheet | Convoluted bellows |
Range of motion | Limited | Large |
Suitable for high pressure applications | No | Yes |
Flexibility | Highly flexible | Moderate |
Applications | Control valves, pumps | Steering systems, actuators |
Lifespan | Limited | Longer |
Longer | Less expensive | More expensiv |
GENERAL SEALTECH was established in 2007, specializing in the production of high-precision silicone rubber sealing products. The main products include Rubber diaphragms,Gas meter diaphragms,Diaphragm Valve pump Diaphragms,Solenoid Pulse Valve Diaphragms,Turbo Actuator Waste-gate Diaphragms,Teflon / PTFE Diaphragm, etc. Widely used in industries such as Battery industry,automotive industry,chemical industry,Food processing industry.
We firmly believe that only excellent quality can win the trust of customers in the fierce market. Our products have been exported to regions such as Europe,Oceania,Africa.And it has been loved by local customers.