What is a rubber diaphragm?
A rubber diaphragm is a flexible, thin sheet made of rubber that is used to separate two substances or spaces while allowing for movement or transfer of pressure. It is commonly used in a variety of industries such as automotive, aerospace, medical, and household appliances.
Production of a rubber diaphragm involves several steps that require specialized equipment and expertise. In this article, we will delve into the process of producing a rubber diaphragm, the materials used, and the industries where it is commonly used.
Materials Used in Rubber Diaphragm Production
The most common material used in the production of rubber diaphragms is synthetic rubber, also known as elastomer. This type of rubber is made from petroleum-derived hydrocarbons and is designed to be more durable and resistant to heat and chemicals than natural rubber. The most commonly used elastomers in diaphragm production include neoprene, nitrile, EPDM, and silicone.
Neoprene is a synthetic rubber that is often used for its resistance to oils, solvents, and weather conditions. Nitrile, also known as Buna-N or NBR, is a type of synthetic rubber that is highly resistant to oils, fuels, and chemicals. EPDM, or ethylene propylene diene monomer, is a synthetic rubber that is commonly used in diaphragms for its excellent resistance to ozone, weather, and heat. Silicone, on the other hand, is a synthetic rubber that is highly resistant to extreme temperatures and offers good electrical insulation properties.
Other materials that may be used in the production of rubber diaphragms include fabric reinforcement, metal or plastic inserts, and adhesives for bonding layers together.
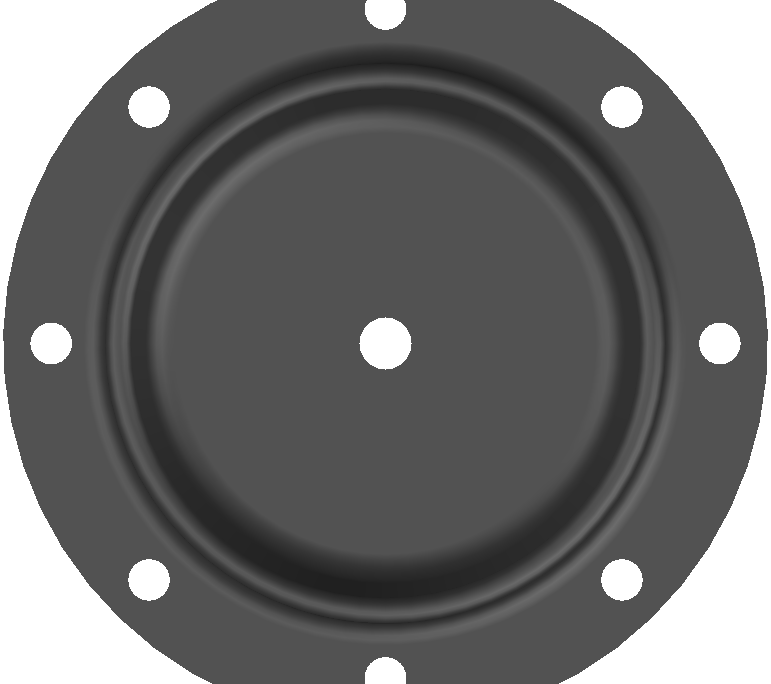
rubber diaphragm
Production Process
The production of a rubber diaphragm can be divided into five main steps: mixing, calendering, molding, curing, and trimming/finishing.
1. Mixing – The first step in producing a rubber diaphragm is to mix the desired elastomer with other ingredients such as vulcanizing agents, fillers, and pigments. This process, also known as compounding, is critical as it determines the physical properties of the final product.
2. Calendering – After the rubber compound is mixed, it is then run through a series of rollers, known as a calender, to create a uniform sheet of the desired thickness. This sheet is often reinforced with layers of fabric or other materials to improve its strength and durability.
3. Molding – Once the sheet is formed, it is then placed into a mold that has the desired shape and design of the diaphragm. The mold is then closed, and the rubber is compressed into the mold using heat and pressure. This process is known as compression molding and is the most common method used in diaphragm production.
4. Curing – After molding, the diaphragm is then transferred to a curing oven where it is heated to a specific temperature for a specific amount of time. This process, known as vulcanization, helps the rubber compound to cross-link, making it stronger, more flexible, and more resistant to heat and chemicals.
5. Trimming/Finishing – The final step in diaphragm production involves trimming the excess material and adding any additional finishing touches, such as cutting holes for fittings or bonding metal or plastic inserts. The diaphragm may also undergo post-curing treatments to further enhance its physical and mechanical properties.
Industries and Applications
Rubber diaphragms have a wide range of applications in various industries due to their flexibility, durability, and resistance to heat and chemicals. Some of the most common applications of rubber diaphragms include:
1. Automotive – Rubber diaphragms are commonly used in the automotive industry for fuel pumps, carburetors, and engine control valves.
2. Aerospace – In the aerospace industry, rubber diaphragms are used in fuel systems, hydraulic systems, and pneumatic systems.
3. Medical – Rubber diaphragms are also used in medical devices such as pumps, valves, and actuators, as well as in respiratory therapy equipment.
4. Household Appliances – Household appliances such as dishwashers, washing machines, and refrigerators use rubber diaphragms in their water inlet and drain valves.
5. Industrial – In the industrial sector, rubber diaphragms are used in pumps, valves, pressure switches, and other applications that require precise control of fluids and gases.
Benefits of Rubber Diaphragms
Rubber diaphragms offer several advantages over other materials, making them the preferred choice in various industries. Some of these benefits include:
1. Flexibility – Rubber diaphragms are highly flexible, allowing them to deform and change shape in response to pressure or movement.
2. Durability – The use of synthetic rubber makes diaphragms highly durable, able to withstand high pressures, temperatures, and exposure to chemicals and oils.
3. Resistance to Heat and Chemicals – Rubber diaphragms are highly resistant to heat, ozone, weather, and a wide range of chemicals, making them suitable for use in extreme environments.
4. Cost-effective – Diaphragms are relatively inexpensive to produce, making them a cost-effective option for various applications.
GENERAL SEALTECH LIMITED is located in Hangzhou, Zhejiang Province, China. We can provide a variety of diaphragm products for you to choose from to meet your needs. We are committed to maintaining the highest quality standards to meet the needs of our customers. Our company is a production-oriented enterprise engaged in the design, development, manufacturing, and sales of diaphragm products.
The technical backbone of the company has more than 10 years of work experience in product development, mold design, material formulation, production quality management, and has cooperation experience with OEMs and ODMs of multiple large enterprises. Our products mainly include LPG CNG Diaphragm,Turbo Actuator Waste-gate Diaphragms,Rolling diaphragm,Solenoid Pulse Valve Diaphragms,Diaphragm Valve pump Diaphragms,Teflon / PTFE Diaphragm, etc. Our products are widely used in fields such as automotive industry,Biomedical field,Food processing industry.
The rubber diaphragm industry is a rapidly growing sector, with a forecasted CAGR of 6% from 2021 to 2026. This growth can be attributed to the increasing demand for rubber diaphragms in various industries such as automotive, aerospace, medical, and oil & gas.
Import and Export Data:
According to the World Integrated Trade Solution (WITS) database, the global imports of rubber diaphragms were valued at USD 4.3 billion in 2020, with a significant increase from USD 3.8 billion in 2019. The top importers of rubber diaphragms include the United States, Germany, China, Japan, and the United Kingdom.
On the other hand, the global exports of rubber diaphragms were valued at USD 3.8 billion in 2020, with a slight decrease from USD 4.1 billion in 2019. The top exporters of rubber diaphragms include Germany, China, Japan, the United States, and Italy.
Development Prospects:
The increasing demand for rubber diaphragms in various industries is expected to drive the growth of the market in the coming years. The automotive industry, in particular, is a major consumer of rubber diaphragms. The growing production and sales of automobiles, especially in developing countries, is expected to boost the demand for rubber diaphragms.
Moreover, the increasing use of rubber diaphragms in medical devices, such as insulin pumps, ventilators, and valves, is also expected to drive the market growth. The rising demand for these devices due to the aging population and the prevalence of chronic diseases is further expected to fuel the demand for rubber diaphragms.
Additionally, the growing use of rubber diaphragms in oil & gas applications, such as control valves, pumps, and compressors, is expected to create new opportunities for the market players. The increasing investments in oil & gas exploration and production activities, particularly in emerging economies, is further expected to support market growth.
With the ongoing development of new technologies and materials, the market for rubber diaphragms is also witnessing a shift towards more advanced and efficient products. Manufacturers are investing in research and development to improve the performance and durability of rubber diaphragms, which is expected to drive the market growth.