What is rubber diaphragm?
Rubber diaphragm is a flexible membrane made from various types of rubber materials, such as natural rubber, synthetic rubber, or silicone rubber. It is used in a wide range of applications, from industrial to medical, due to its durability, strength, and flexibility. In this article, we will explore the features, uses, and benefits of rubber diaphragm.
Features of Rubber Diaphragm
Rubber diaphragms have some unique characteristics that make them suitable for various applications.
These features include:
1. Flexibility: Rubber is a highly flexible material, making rubber diaphragms ideal for applications that require repeated movements or changes in shape.
2. Resilience: Rubber is a resilient material, meaning it can return to its original shape after being stretched or compressed. This quality makes rubber diaphragms long-lasting and able to withstand high pressures without sustaining permanent damage.
3. Chemical Resistance: Rubber diaphragms are resistant to a wide range of chemicals, including oils, greases, acids, and alkalis. This makes them suitable for use in harsh environments, where exposure to chemicals is common.
4. Temperature Resistance: Depending on the type of rubber used, rubber diaphragms can withstand extreme temperatures, making them suitable for use in both hot and cold environments.
Uses of Rubber Diaphragm
1. Pumps and Valves: One of the most common uses of rubber diaphragms is in pumps and valves. These devices require a flexible and durable material to control the flow of fluids and gases, making rubber diaphragms an ideal choice.
2. Automotive Industry: Rubber diaphragms are also widely used in the automotive industry. They can be found in fuel pumps, carburetors, and emission control systems, among others.
3. Medical Equipment: Many medical devices, such as ventilators and blood pressure gauges, use rubber diaphragms. The flexibility and durability of rubber make it a safe and effective material for sensitive medical applications.
4. Industrial Applications: Rubber diaphragms are used in various industrial applications, including actuators, control valves, and regulators. They can withstand high pressures and extreme temperatures, making them suitable for use in harsh environments.
5. Food and Beverage Industry: Rubber diaphragms are commonly used in food and beverage processing equipment, such as pumps and valves. The chemical and temperature resistance of rubber make it a safe and reliable material for these applications.
Benefits of Rubber Diaphragm
1. Cost-Effective: Rubber diaphragms are a cost-effective solution for many applications. They are relatively inexpensive to produce and have a long lifespan, reducing the need for frequent replacements.
2. Low Maintenance: Rubber diaphragms are low maintenance, as they can withstand wear and tear without requiring frequent repairs.
3. Versatility: Rubber diaphragms are highly versatile and can be custom-made to fit specific requirements. This makes them suitable for a wide range of applications, from simple to complex.
4. Durability: Rubber diaphragms have a high resistance to wear and tear, making them highly durable. They can withstand high pressures, extreme temperatures, and exposure to chemicals, ensuring a longer lifespan.
5. Efficiency: Due to their flexibility and resilience, rubber diaphragms can improve the efficiency and performance of various devices and equipment. They can maintain a tight seal and control the flow of fluids and gases effectively.
Rubber diaphragms are an essential component in various industries, playing a crucial role in controlling the flow of fluids and gases. Their flexibility, durability, and versatility make them a popular choice for many applications, from pumps and valves to medical equipment and food processing. With continued advancements in technology and materials, rubber diaphragms will continue to be an integral part of many industries for years to come.
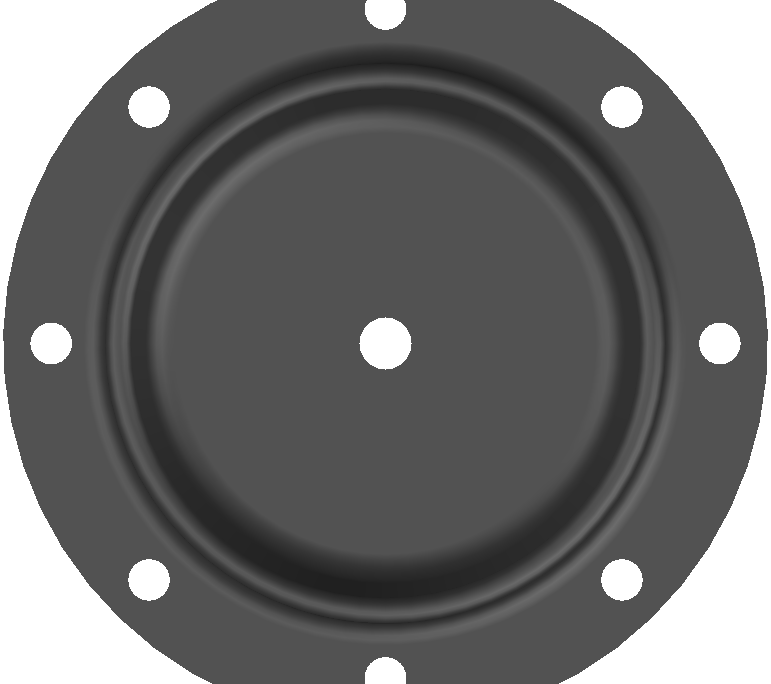
rubber diaphragm
What is the function of the rubber diaphragm?
Rubber diaphragms are flexible rubber membranes, sometimes reinforced with fabric, strategically placed to prevent unwanted transfer of substances between two places by creating a seal. They can be used to separate two gasses, two liquids, or one gas and one liquid that should not mix.
What material is used for fuel pump diaphragms?
These materials can be grouped into three primary families: rubber, thermoplastic elastomer(TPE) and polytetrafluoroethylene (PTFE).
These primary materials are available in a variety of designs – each offering unique benefits depending on the application and the characteristics of the product being pumped.
What is the manufacturing process of a diaphragm?
The manufacturing process of a diaphragm typically involves the following steps:
1. Selection of Materials: The first step is to select the materials for the diaphragm. Depending on the application, materials such as rubber, silicone, plastic, or metal may be used.
2. Cutting: The selected material is cut into the desired shape using techniques such as die cutting, laser cutting, or water jet cutting.
3. Molding: If the diaphragm requires a complex shape, it may be molded using a process such as injection molding or compression molding.
4. Coating: Some diaphragms may require a coating on one or both sides to improve their performance or durability. This can include processes such as applying a silicone coating or using a chemical coating method.
5. Bonding: If the diaphragm is made of multiple layers of material, they may need to be bonded together using adhesives or heat bonding.
6. Forming: The diaphragm may need to be shaped or formed into its final shape using techniques such as heat forming, vacuum forming, or mechanical forming.
7. Punching: Holes or slots may need to be punched into the diaphragm to allow for the flow of fluids or gases. This can be done using a punch and die or a laser cutting machine.
8. Quality Control: Throughout the manufacturing process, quality checks are performed to ensure that the diaphragm meets the required specifications and standards.
9. Finishing: The final step may involve trimming excess material, smoothing edges, or applying a protective coating to the diaphragm.
10. Packaging: The finished diaphragm is packaged and labeled for shipping to the customer.
GENERAL SEALTECH is engaged in the research, development, production, process, marketing and trade of diaphragms. We have experienced and professional staff members. We have strong mold development capabilities and high precision instruments and equipment.
We specialize in the production of Diaphragm Valve pump Diaphragms,LPG CNG Diaphragm,Rolling diaphragm,Gas meter diaphragms,Solenoid Pulse Valve Diaphragms,Rubber diaphragms,etc.After more than 15 years of pioneering venture, we have already become a professional company in the field. We follow the “leading technology, improving quality” principle.
FAQs Guide
2.What is the role of rubber diaphragm in controlling the flow of aggressive or corrosive chemicals in chemical processing applications?
3.Can rubber diaphragm be used in medical devices, and what biocompatibility standards do they need to meet?
4.Do rubber diaphragm require maintenance or replacement over time, and what are the signs that indicate the need for replacement?
5.How do rubber diaphragm perform in applications where flexibility and rapid response to pressure changes are crucial?
6.What are the common materials used in diaphragm manufacturing, and how do they impact the diaphragm’s performance?
7.What are the considerations for choosing between elastomeric rubber diaphragm and non-elastomeric rubber diaphragm for specific applications?
8.How does the thickness of a rubber diaphragm affect its flexibility and pressure resistance?
1.Are there rubber diaphragm designed for quick and easy replacement to minimize downtime in industrial processes?
Yes, there are diaphragms designed for quick and easy replacement to minimize downtime in industrial processes. These diaphragms are typically made of materials such as rubber, silicone, or PTFE, and are designed to be easily replaced without the need for tools or special equipment. Additionally, some diaphragms are designed with quick-connect fittings to further reduce downtime.
2.What is the role of rubber diaphragm in controlling the flow of aggressive or corrosive chemicals in chemical processing applications?
Diaphragms are used to control the flow of aggressive or corrosive chemicals in chemical processing applications. They act as a barrier between the chemical and the process equipment, preventing the chemical from coming into contact with the equipment and causing corrosion or other damage. Diaphragms are also used to regulate the flow of the chemical, allowing for precise control of the process.
3.Can rubber diaphragm be used in medical devices, and what biocompatibility standards do they need to meet?
Yes, diaphragms can be used in medical devices. The biocompatibility standards that diaphragms need to meet depend on the application and the intended use of the device. Generally, diaphragms used in medical devices must meet the requirements of ISO 10993-1, which outlines the general requirements for biocompatibility. Additionally, depending on the application, the diaphragm may need to meet additional requirements, such as those outlined in ISO 10993-5 for cytotoxicity, ISO 10993-10 for irritation and sensitization, and ISO 10993-11 for hemocompatibility.
4.Do rubber diaphragm require maintenance or replacement over time, and what are the signs that indicate the need for replacement?
Yes, diaphragms require maintenance and replacement over time. Signs that indicate the need for replacement include a decrease in sound quality, a decrease in volume, and a decrease in the overall performance of the diaphragm. Additionally, if the diaphragm is damaged or cracked, it should be replaced immediately.
5.How do rubber diaphragm perform in applications where flexibility and rapid response to pressure changes are crucial?
Diaphragms are ideal for applications where flexibility and rapid response to pressure changes are crucial. They are designed to flex and move in response to pressure changes, allowing them to quickly adjust to changing conditions. This makes them ideal for use in applications such as pumps, valves, and other pressure-sensitive systems. Additionally, diaphragms are often used in applications where a tight seal is required, such as in fuel tanks and hydraulic systems.
6.What are the common materials used in diaphragm manufacturing, and how do they impact the diaphragm’s performance?
Common materials used in diaphragm manufacturing include rubber, silicone, neoprene, polyurethane, and polyester. Each material has its own unique properties that can affect the performance of the diaphragm.
Rubber is a popular choice for diaphragms due to its flexibility and durability. It is also resistant to heat, chemicals, and abrasion. However, rubber can be prone to cracking and tearing over time.
Silicone is a synthetic material that is highly resistant to heat and chemicals. It is also very flexible and can be used in a wide range of applications. However, silicone can be prone to tearing and is not as durable as rubber.
Neoprene is a synthetic rubber material that is highly resistant to heat, chemicals, and abrasion. It is also very flexible and can be used in a wide range of applications. However, neoprene can be prone to cracking and tearing over time.
Polyurethane is a synthetic material that is highly resistant to heat, chemicals, and abrasion. It is also very flexible and can be used in a wide range of applications. However, polyurethane can be prone to cracking and tearing over time.
Polyester is a synthetic material that is highly resistant to heat, chemicals, and abrasion. It is also very flexible and can be used in a wide range of applications. However, polyester can be prone to cracking and tearing over time.
7.What are the considerations for choosing between elastomeric rubber diaphragm and non-elastomeric rubber diaphragm for specific applications?
We are a professional rubber diaphragm manufacturer, and the factors we consider include:
1. Cost: Elastomeric diaphragms are typically more expensive than non-elastomeric diaphragms.
2. Durability: Elastomeric diaphragms are more durable and can withstand higher pressures and temperatures than non-elastomeric diaphragms.
3. Chemical Compatibility: Elastomeric diaphragms are more resistant to chemical attack than non-elastomeric diaphragms.
4. Flexibility: Elastomeric diaphragms are more flexible than non-elastomeric diaphragms, allowing them to be used in applications where a tight seal is required.
5. Performance: Elastomeric diaphragms are better at maintaining a seal over time than non-elastomeric diaphragms.
8.How does the thickness of a rubber diaphragm affect its flexibility and pressure resistance?
The thicker the diaphragm, the less flexible it will be and the more pressure it will be able to resist. This is because thicker diaphragms are more rigid and can withstand higher pressures without deforming. Thinner diaphragms are more flexible and can deform more easily under pressure, but they are also less resistant to pressure.