How is the rubber diaphragm produced?
Rubber diaphragm is typically produced through a process called compression molding. This involves placing a pre-measured amount of rubber compound into a heated mold cavity and then applying pressure to the rubber until it takes the shape of the mold. The rubber is then cooled and removed from the mold.
How many types of rubber diaphragm are there?
There are three main types of rubber diaphragms: flat, bellows, and convoluted. Each type has its own unique characteristics and applications.
The main function of the rubber diaphragm
A rubber diaphragm is a flexible, airtight membrane that is used to separate two different areas. It is commonly used in a variety of applications, such as pumps, valves, and other mechanical devices. The diaphragm is made of a flexible rubber material that is designed to be able to withstand pressure and temperature changes. The diaphragm is designed to be able to move in response to pressure changes, allowing it to act as a valve or pump. The diaphragm is also used to create a seal between two different areas, preventing the flow of air or other substances between them. The diaphragm is also used to absorb shock and vibration, making it ideal for use in a variety of applications.
How does the rubber diaphragm manufacturer produce the rubber diaphragm?
The rubber diaphragm manufacturer typically begins the production process by creating a rubber compound that is designed to meet the specific requirements of the application. This rubber compound is then mixed with a curing agent and other additives to create a rubber sheet. The rubber sheet is then cut into the desired shape and size of the diaphragm. The edges of the diaphragm are then trimmed and the diaphragm is cured in an oven. After curing, the diaphragm is inspected for quality and then packaged for shipment.
How to purchase rubber diaphragm from China?
1. Research potential suppliers: Start by researching potential suppliers in China. You can use online resources such as Alibaba, Global Sources, and Made-in-China to find suppliers that offer rubber diaphragms.
2. Contact suppliers: Once you have identified potential suppliers, contact them to inquire about their products and services. Ask for samples and pricing information.
3. Negotiate terms: Negotiate terms with the supplier, such as payment terms, delivery times, and quality assurance.
4. Place an order: Once you have agreed on terms, place an order with the supplier. Make sure to provide clear instructions and payment information.
5. Receive and inspect the product: Once the product has been delivered, inspect it to make sure it meets your expectations. If there are any issues, contact the supplier to resolve them.
Design prototype of rubber diaphragm rubber diaphragm
Prototype:
Material: Natural rubber
Shape: Round
Diameter: 2 inches
Thickness: 0.25 inches
Surface Finish: Smooth
Mounting: Bolt holes on the circumference
Features: Reinforced edges for increased durability and strength
rubber diaphragm manufacturer need to have the following production equipment
Rubber diaphragm manufacturers typically need the following production equipment:
1. Rubber mixing machine: This machine is used to mix the rubber compound ingredients together to create the desired rubber diaphragm.
2. Compression molding machine: This machine is used to shape the rubber diaphragm into the desired shape and size.
3. Curing oven: This machine is used to cure the rubber diaphragm to ensure it is durable and long-lasting.
4. Testing equipment: This equipment is used to test the rubber diaphragm for quality assurance.
5. Cutting machine: This machine is used to cut the rubber diaphragm into the desired size and shape.
Information reference for the distribution map of rubber diaphragm manufacturer in China’s industrial chain
1. China Rubber Industry Association: The China Rubber Industry Association provides information on the distribution of rubber diaphragm manufacturers in China’s industrial chain. The association’s website provides a list of rubber diaphragm manufacturers in China, as well as contact information for each manufacturer.
2. China Rubber Industry Network: The China Rubber Industry Network provides a comprehensive directory of rubber diaphragm manufacturers in China. The directory includes contact information for each manufacturer, as well as a map of their locations.
3. China Rubber Industry Association: The China Rubber Industry Association provides a detailed map of the distribution of rubber diaphragm manufacturers in China’s industrial chain. The map includes the locations of each manufacturer, as well as contact information for each manufacturer.
4. China Rubber Industry Association: The China Rubber Industry Association provides a detailed report on the distribution of rubber diaphragm manufacturers in China’s industrial chain. The report includes information on the number of manufacturers, their locations, and contact information for each manufacturer.
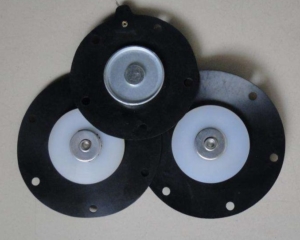
Solenoid Pulse Valve Diaphragms
Some suggestions for improving the utilization rate of equipment for rubber diaphragm manufacturer
1. Implement preventive maintenance: Regularly inspect and maintain equipment to ensure that it is in good working condition and can be used for a longer period of time.
2. Invest in new technology: Invest in new technology that can help increase the efficiency of the equipment and reduce downtime.
3. Automate processes: Automate processes to reduce manual labor and increase the utilization rate of the equipment.
4. Improve training: Provide training to employees on how to use the equipment properly and efficiently.
5. Reduce waste: Reduce waste by using the equipment more efficiently and reducing the amount of scrap material produced.
6. Monitor usage: Monitor the usage of the equipment to identify areas where improvements can be made.
7. Utilize idle time: Utilize idle time by using the equipment for other tasks or by renting it out to other companies.
What are the advantages of rubber diaphragm manufacturers with large-scale production compared with small-scale production?
1. Cost savings: Large-scale production allows for economies of scale, which can result in lower costs for materials, labor, and overhead.
2. Increased efficiency: Large-scale production allows for more efficient use of resources, resulting in higher output and faster turnaround times.
3. Improved quality: With larger production runs, manufacturers can take advantage of better quality control measures, resulting in higher quality products.
4. Greater flexibility: Large-scale production allows for more flexibility in terms of product design and customization.
5. Increased market reach: With larger production runs, manufacturers can reach a wider market, resulting in increased sales and profits.
rubber diaphragm manufacturer raw material supply chain development and maintenance experience sharing
1. Develop a reliable supply chain: Developing a reliable supply chain is essential for any rubber diaphragm manufacturer. This includes identifying and selecting reliable suppliers, negotiating contracts, and establishing long-term relationships with them.
2. Establish quality control standards: Quality control is essential for any rubber diaphragm manufacturer. Establishing quality control standards and procedures will ensure that the products meet customer requirements and expectations.
3. Monitor supplier performance: It is important to monitor supplier performance to ensure that they are meeting the quality standards and deadlines. This can be done through regular audits and reviews.
4. Utilize technology: Technology can be used to streamline the supply chain and improve efficiency. This includes using software to track orders, monitor inventory, and manage supplier relationships.
5. Invest in research and development: Investing in research and development can help rubber diaphragm manufacturers stay ahead of the competition. This includes researching new materials, processes, and technologies that can improve the quality and performance of the products.
When purchasing rubber diaphragm from Chinese rubber diaphragm manufacturer, you need to pay attention to the following payment and delivery terms
1. Payment Terms: Most Chinese rubber diaphragm manufacturers accept payment by T/T (Telegraphic Transfer) or L/C (Letter of Credit).
2. Delivery Terms: Most Chinese rubber diaphragm manufacturers offer FOB (Free On Board) or CIF (Cost, Insurance and Freight) delivery terms.
3. Quality Control: Make sure to ask the Chinese rubber diaphragm manufacturer about their quality control procedures and certifications.
4. Lead Time: Ask the Chinese rubber diaphragm manufacturer about their lead time for production and delivery.
5. Warranty: Ask the Chinese rubber diaphragm manufacturer about their warranty policy.
Who invented the production process of rubber diaphragm manufacturers at first?
The first rubber diaphragm manufacturer was Charles Goodyear, who invented the vulcanization process in 1839. This process allowed rubber to be heated and mixed with sulfur, which made it more durable and resistant to heat and cold. This process is still used today by rubber diaphragm manufacturers.
Several update iterations experienced by rubber diaphragm manufacturer in production technology
1. Automation: Automating the production process with robotic arms and other automated machinery to reduce labor costs and increase efficiency.
2. Quality Control: Implementing quality control measures to ensure that the diaphragms produced meet the required standards.
3. Material Selection: Selecting the right materials for the diaphragms to ensure that they are durable and long-lasting.
4. Design Optimization: Optimizing the design of the diaphragms to reduce production costs and improve performance.
5. Process Improvement: Improving the production process to reduce waste and increase efficiency.
6. Cost Reduction: Reducing the cost of production by using more efficient methods and materials.
7. Lean Manufacturing: Implementing lean manufacturing principles to reduce waste and increase efficiency.
The production process of the rubber diaphragm manufacturer
1. Raw material preparation: The rubber diaphragm manufacturer will select the appropriate raw materials according to the customer’s requirements, and then cut the raw materials into the required size.
2. Compounding: The rubber diaphragm manufacturer will mix the raw materials with the appropriate amount of additives and fillers, and then use a rubber mixer to mix them into a uniform compound.
3. Molding: The rubber diaphragm manufacturer will use a molding machine to shape the rubber compound into the desired shape and size.
4. Curing: The rubber diaphragm manufacturer will then place the molded rubber parts in a curing oven to cure them.
5. Finishing: The rubber diaphragm manufacturer will then inspect the parts for any defects and trim any excess material.
6. Packaging: The rubber diaphragm manufacturer will then package the parts for shipment.
rubber diaphragm manufacturer production process management
Rubber diaphragm manufacturers typically use a production process management system to ensure that their products are of the highest quality. This system typically includes the following steps:
1. Quality Control: Quality control is the first step in the production process. The manufacturer must ensure that all raw materials used in the production process meet the required standards. This includes testing the raw materials for any contaminants or defects.
2. Design and Development: The manufacturer must design and develop the rubber diaphragm according to the customer’s specifications. This includes selecting the right materials, designing the shape and size, and ensuring that the diaphragm meets the customer’s requirements.
3. Production: The manufacturer must then produce the rubber diaphragm according to the design and specifications. This includes selecting the right machinery and tools, setting up the production line, and ensuring that the production process is efficient and cost-effective.
4. Quality Assurance: The manufacturer must then perform quality assurance tests on the rubber diaphragm to ensure that it meets the customer’s requirements. This includes testing the diaphragm for any defects or contaminants.
5. Delivery: The manufacturer must then deliver the rubber diaphragm to the customer. This includes ensuring that the diaphragm is properly packaged and shipped in a timely manner.
By following these steps, rubber diaphragm manufacturers can ensure that their products are of the highest quality and meet the customer’s requirements.
The production of rubber diaphragm manufacturer needs to meet the following environmental protection conditions
1. Adhere to the principle of environmental protection and energy conservation, and strictly abide by the relevant environmental protection laws and regulations.
2. Establish a sound environmental protection management system, formulate environmental protection management regulations, and implement them.
3. Strengthen environmental protection education and training for employees, and improve their environmental protection awareness.
4. Strengthen the monitoring of environmental pollution sources, and take effective measures to reduce and control environmental pollution.
5. Strengthen the management of hazardous waste, and ensure the safe disposal of hazardous waste.
6. Strengthen the management of noise and vibration, and take effective measures to reduce noise and vibration.
7. Strengthen the management of water resources, and take effective measures to reduce water consumption.
8. Strengthen the management of air pollution, and take effective measures to reduce air pollution.
9. Strengthen the management of solid waste, and take effective measures to reduce solid waste.
10. Strengthen the management of hazardous chemicals, and take effective measures to reduce the use of hazardous chemicals.
Compared with 10 years ago, the manufacturing process of rubber diaphragm manufacturer has the following improvements
1. Automation: Automation has been widely adopted in the manufacturing process of rubber diaphragm manufacturers, allowing for faster and more efficient production.
2. Quality Control: Quality control has been improved significantly, with the introduction of advanced testing equipment and techniques.
3. Materials: New materials have been developed to improve the performance of rubber diaphragms, such as silicone and fluorocarbon elastomers.
4. Design: Design has been improved to create more efficient and reliable rubber diaphragms.
5. Cost Reduction: Cost reduction has been achieved through the use of advanced manufacturing techniques and materials.
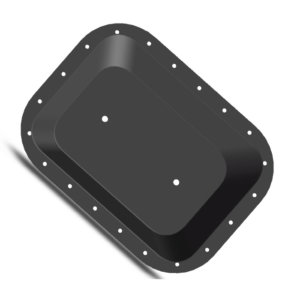
GENERAL SEALTECH LIMITED a rubber diaphragm manufacture. www.rubberdiaphragms.cn
Three plans for rubber diaphragm manufacturers to improve production efficiency
1. Automate Production Processes: Automating production processes can help rubber diaphragm manufacturers to increase production efficiency. Automation can help reduce labor costs, improve accuracy, and reduce waste. Automation can also help to reduce the time it takes to complete a production cycle.
2. Invest in Quality Control: Quality control is essential for rubber diaphragm manufacturers to ensure that their products meet customer expectations. Investing in quality control measures such as testing and inspection can help to reduce the number of defective products and improve production efficiency.
3. Implement Lean Manufacturing Practices: Lean manufacturing practices can help rubber diaphragm manufacturers to reduce waste and improve production efficiency. Lean manufacturing focuses on eliminating waste and improving efficiency by streamlining processes and eliminating unnecessary steps. Implementing lean manufacturing practices can help rubber diaphragm manufacturers to reduce costs and improve production efficiency.
Analysis of the cost that the rubber diaphragm manufacturer pays for the implementation of new product research and development every year
The cost of implementing new product research and development for a rubber diaphragm manufacturer can vary greatly depending on the size and scope of the project. Generally, the cost of research and development for a new product can include the following:
1. Personnel costs: the salaries of the research and development team, as well as any additional personnel needed to support the project.
2. Equipment costs: the cost of any specialized equipment needed to develop the new product.
3. Materials costs: the cost of any raw materials needed to create the new product.
4. Testing costs: the cost of any testing needed to ensure the product meets the desired specifications.
5. Regulatory costs: the cost of any regulatory approvals needed to bring the product to market.
6. Marketing costs: the cost of any marketing efforts needed to promote the new product.
The total cost of implementing new product research and development for a rubber diaphragm manufacturer will depend on the size and scope of the project, as well as the resources available to the company.
rubber diaphragm manufacturer service and quality system
A rubber diaphragm manufacturer should have a quality system in place to ensure that their products meet the highest standards of quality. This system should include a quality assurance program, a quality control program, and a quality management system. The quality assurance program should include a process for testing and inspecting the diaphragms to ensure that they meet the customer’s specifications. The quality control program should include a process for tracking and monitoring the performance of the diaphragms over time. The quality management system should include a process for documenting and analyzing customer feedback and complaints. The manufacturer should also have a customer service system in place to ensure that customers are satisfied with their purchase.
What are the services of rubber diaphragm manufacturer?
1. Design and manufacture of custom rubber diaphragms for a variety of applications.
2. Supply of standard and custom rubber diaphragms for a variety of industries.
3. Testing and validation of rubber diaphragms for quality assurance.
4. Repair and maintenance of rubber diaphragms.
5. Consultancy services for rubber diaphragm selection and application.
6. Supply of rubber diaphragm components such as seals, gaskets, and O-rings.
7. Supply of rubber diaphragm materials such as silicone, EPDM, and neoprene.
rubber diaphragm manufacturer need to pay attention to the following points when establishing their own rubber diaphragm dealer channels
1. Establish a good relationship with the rubber diaphragm manufacturer. The rubber diaphragm manufacturer should establish a good relationship with the rubber diaphragm dealer, and the two sides should have a good understanding of each other’s needs and interests.
2. Establish a good reputation. The rubber diaphragm manufacturer should establish a good reputation in the market, so that the rubber diaphragm dealers can trust them and be willing to cooperate with them.
3. Establish a good communication channel. The rubber diaphragm manufacturer should establish a good communication channel with the rubber diaphragm dealers, so that they can communicate with each other in a timely manner and understand each other’s needs.
4. Provide good service. The rubber diaphragm manufacturer should provide good service to the rubber diaphragm dealers, so that they can be satisfied with the service and be willing to cooperate with them.
5. Establish a good marketing strategy. The rubber diaphragm manufacturer should establish a good marketing strategy, so that they can promote their products and services to the rubber diaphragm dealers.
R&D direction of rubber diaphragm manufacturer industry
1. Develop new materials: Develop new materials with better performance and lower cost to meet the needs of different customers.
2. Improve production process: Improve the production process to reduce the cost and improve the quality of rubber diaphragms.
3. Improve product design: Improve the design of rubber diaphragms to meet the needs of different customers.
4. Develop new technologies: Develop new technologies to improve the performance of rubber diaphragms and reduce the cost.
5. Improve customer service: Improve customer service to provide better service and support to customers.
6. Develop new applications: Develop new applications for rubber diaphragms to meet the needs of different customers.
7. Develop new markets: Develop new markets for rubber diaphragms to expand the customer base.
How to improve the quality of rubber diaphragm manufacturers
1. Improve the production process: The production process of rubber diaphragm manufacturers should be improved to ensure the quality of the products. The production process should be optimized to reduce the production cost and improve the quality of the products.
2. Improve the quality control system: The quality control system should be improved to ensure the quality of the products. The quality control system should be designed to detect the defects in the products and take corrective measures to improve the quality of the products.
3. Improve the raw materials: The raw materials used in the production of rubber diaphragm should be of high quality to ensure the quality of the products. The raw materials should be tested and certified to ensure the quality of the products.
4. Improve the production equipment: The production equipment should be improved to ensure the quality of the products. The production equipment should be upgraded to ensure the efficient production of the products.
5. Improve the customer service: The customer service should be improved to ensure the satisfaction of the customers. The customer service should be designed to provide timely and efficient services to the customers.
Customer group and service level of rubber diaphragm manufacturer
The customer group for a rubber diaphragm manufacturer would likely include industrial and commercial businesses that require rubber diaphragms for their products or processes. The service level of the manufacturer would depend on the specific needs of the customer. The manufacturer may offer custom design and manufacturing services, as well as a range of standard products. They may also provide technical support and after-sales services.
After-sales compensation terms for rubber diaphragm manufacturer
1. Warranty: The rubber diaphragm manufacturer should provide a warranty period of at least one year from the date of purchase. During this period, the manufacturer should repair or replace any defective parts free of charge.
2. Replacement: If the rubber diaphragm fails to meet the customer’s requirements, the manufacturer should provide a replacement part free of charge.
3. Refund: If the customer is not satisfied with the product, the manufacturer should provide a full refund within 30 days of purchase.
4. Technical Support: The manufacturer should provide technical support to the customer in case of any problems with the product.
5. Spare Parts: The manufacturer should provide spare parts for the rubber diaphragm at a reasonable cost.
What services are included in the rubber diaphragm manufacturer’s after-sales service?
The after-sales service of a rubber diaphragm manufacturer typically includes:
1. Technical support and advice on product selection and application.
2. On-site installation and commissioning of the product.
3. Regular maintenance and repair services.
4. Replacement parts and components.
5. Training and education on the proper use and maintenance of the product.
6. Troubleshooting and problem-solving assistance.
7. Warranty and guarantee services.
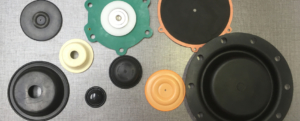
GENERAL SEALTECH LIMITED
Product quality control of rubber diaphragm manufacturer
1. Raw material inspection: The raw materials used in the production of rubber diaphragms must be inspected for quality before they can be used in production. This includes checking for any impurities, contaminants, or other defects that could affect the quality of the finished product.
2. Mold inspection: The molds used to create the rubber diaphragms must be inspected for any defects or irregularities that could affect the quality of the finished product.
3. Production process inspection: The production process must be monitored to ensure that all steps are being followed correctly and that the quality of the finished product is not compromised.
4. Final product inspection: The finished rubber diaphragms must be inspected for any defects or irregularities that could affect the quality of the product. This includes checking for any tears, cracks, or other imperfections.
5. Testing: The rubber diaphragms must be tested for their performance and durability. This includes testing for pressure, temperature, and other factors that could affect the quality of the product.
rubber diaphragm manufacturer’ skill requirements for production operators
Production operators in the rubber diaphragm manufacturing industry must have a variety of skills in order to be successful. These skills include:
1. Knowledge of rubber diaphragm manufacturing processes and techniques.
2. Read and interpret blueprints and technical drawings.
3. Knowledge of safety procedures and regulations.
4. Use hand and power tools.
5. Use measuring instruments such as calipers and micrometers.
6. Troubleshoot and diagnose problems.
7. Work with a variety of materials, including rubber, plastic, and metal.
8. Work with computers and other automated equipment.
9. Ability to work in a team environment.
10. Follow instructions and work with minimal supervision.
What is rubber diaphragm design?
A rubber diaphragm design is a type of mechanical seal that uses a flexible rubber diaphragm to create a seal between two surfaces. The diaphragm is typically made of a rubber material such as neoprene, silicone, or EPDM. The diaphragm is designed to flex and move with the surfaces it is sealing, creating a tight seal that prevents the leakage of fluids or gases. Rubber diaphragm designs are commonly used in pumps, valves, and other fluid control systems.
Classification of rubber diaphragm design styles
1. Flat Diaphragm: This type of diaphragm is the most common and is used in a variety of applications. It is a flat sheet of rubber with a hole in the center for mounting.
2. Bellows Diaphragm: This type of diaphragm is designed to provide a flexible seal between two components. It is typically used in applications where a tight seal is required.