We are engaged in the research, development, production, process, marketing and trade of diaphragms. We have experienced and professional staff members. We have strong mold development capabilities and high precision instruments and equipment. We specialize in the production of Rubber diaphragms, Rolling diaphragms, LPG CNG Diaphragms, Teflon/PTFE Diaphragms,etc.After more than 15 years of pioneering venture, we have already become a professional company in the field. We follow the “leading technology, improving quality” principle. Our products are exported to Europe, America and Southeast Asia.
Diaphragm rubber technology can be widely used in various application fields. It can be used for material control and purification of liquids, steam, air, food, drugs, and other media, as well as isolation, catalysis, and membrane functions.
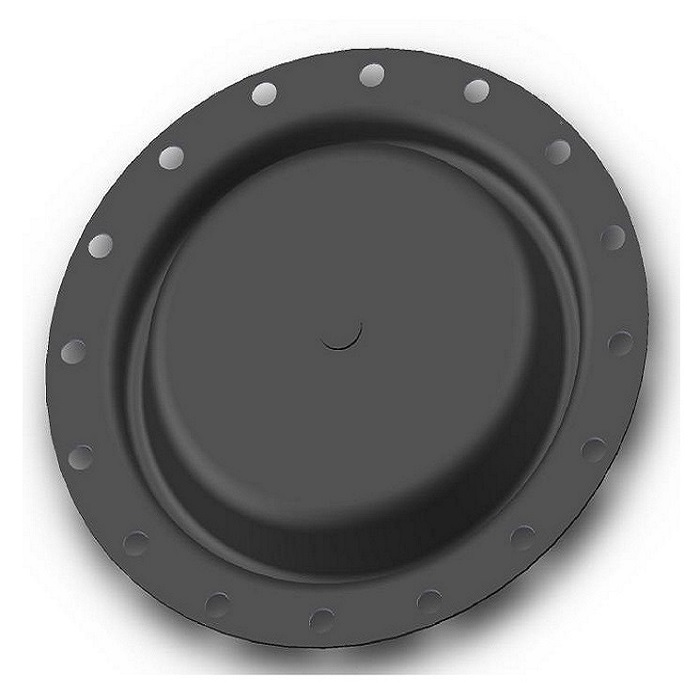
Diaphragm rubber is a universal and flexible sealing component that can provide variable sealing in flow control applications. The rubber diaphragms produced by GENERAL SEALTECH LIMITED are made of various single and composite elastomers, suitable for various industry applications.
The diaphragm is considered the most valuable component to meet all sealing needs, and our diaphragm seals are produced to adapt to any challenging shape and configuration, depending on your application requirements.
Diaphragm rubber is a flexible diaphragm, sometimes reinforced with fabric, strategically placed to prevent unnecessary transfer of material between two places by forming a seal. They can be used to separate two gases, two liquids, or one gas and one liquid that should not be mixed.
In fact, diaphragms come in various shapes and sizes. The thickness depends on the diameter and flexibility of the diaphragm
Membranes can be made of various materials, depending on the final application. Diaphragms have a wide range of applications, but are most commonly used in environments with pressure differences. The diaphragm has low fluid permeability and the ability to bend left and right, making it a sealing solution while providing consistent pressure difference.
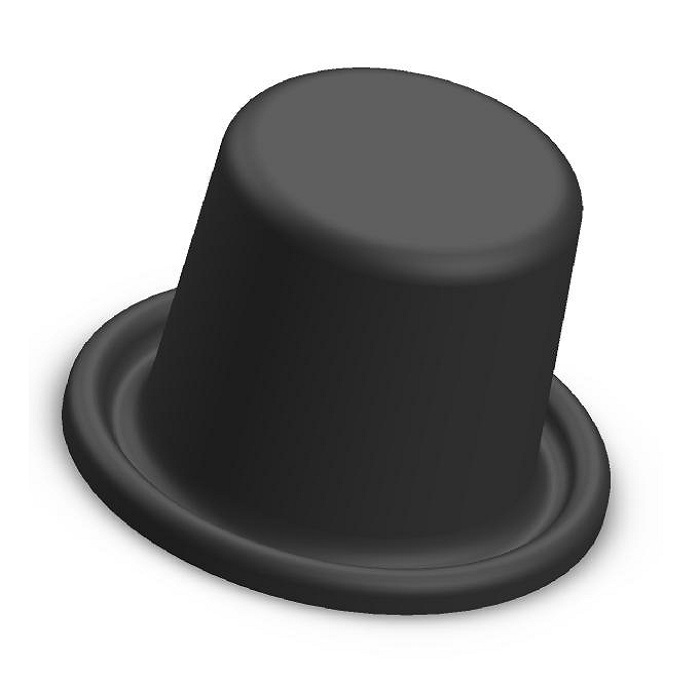
Why choose us?
- 11. We have more than 15 years of industry experience in water treatment.2. High quality products and competitive price.
3. We have professional business personnel and engineers to provide you with type selection assistance and technical support.
Diaphragm rubber–A Guide to Frequently Asked Questions
2.How do diaphragm rubber contribute to the isolation of different process media or gases within a system?
3.How do diaphragms contribute to the precision and accuracy of pressure control and regulation systems?
4.Are there diaphragms designed for use in critical industries such as aerospace and healthcare, and what unique properties do they possess?
5.Do diaphragm rubber have temperature limitations, and how do they perform in extreme temperature conditions?
6.What mechanical and industrial applications can diaphragms be used in?
7.What are the considerations for choosing between elastomeric diaphragms and non-elastomeric diaphragms for specific applications?
8.Are diaphragms suitable for use in applications involving harsh radiation or extreme pressure differentials?
9.Are there diaphragms equipped with built-in sensors for real-time monitoring and feedback in automated systems?
10.Are there diaphragms designed for pulsation dampening or shock absorption in hydraulic systems?
11.How do diaphragm rubber respond to cyclic or pulsating pressure loads, and what is their fatigue life in such conditions?
1.Can diaphragms be used in medical devices, and what biocompatibility standards do they need to meet?
Yes, diaphragms can be used in medical devices. The biocompatibility standards that diaphragms need to meet depend on the application and the intended use of the device. Generally, diaphragms used in medical devices must meet the requirements of ISO 10993-1, which outlines the general requirements for biocompatibility. Additionally, depending on the application, the diaphragm may need to meet additional requirements, such as those outlined in ISO 10993-5 for cytotoxicity, ISO 10993-10 for irritation and sensitization, and ISO 10993-11 for hemocompatibility.
2.How do diaphragm rubber contribute to the isolation of different process media or gases within a system?
diaphragm rubber are used to separate different process media or gases within a system by creating a physical barrier between them. This barrier prevents the media or gases from mixing, thus providing a degree of isolation. Diaphragms are also used to control the flow of media or gases within a system, as they can be designed to open and close in response to pressure or other external factors.
3.How do diaphragms contribute to the precision and accuracy of pressure control and regulation systems?
Diaphragms are used in pressure control and regulation systems to provide a precise and accurate control of pressure. They are used to separate the pressure sensing element from the process fluid, allowing for a more accurate and repeatable measurement of pressure. The diaphragm also acts as a barrier to prevent contamination of the sensing element, which can lead to inaccurate readings. The diaphragm also helps to dampen pressure fluctuations, providing a more stable and consistent pressure control.
4.Are there diaphragms designed for use in critical industries such as aerospace and healthcare, and what unique properties do they possess?
Yes, there are diaphragms designed for use in critical industries such as aerospace and healthcare. These diaphragms are typically made from high-performance materials such as PTFE, FKM, and EPDM, which offer superior chemical and temperature resistance, as well as excellent durability and strength. Additionally, these diaphragms are designed to meet the stringent requirements of these industries, such as tight tolerances, high-pressure ratings, and low-leakage rates.
5.Do diaphragm rubber have temperature limitations, and how do they perform in extreme temperature conditions?
diaphragm rubber do have temperature limitations, and their performance in extreme temperature conditions can vary depending on the material used. Generally, diaphragms are designed to operate within a temperature range of -40°F to +250°F (-40°C to +121°C). In extreme temperature conditions, the diaphragm may become brittle and crack, or the material may become too soft and lose its shape. Additionally, the diaphragm may become distorted due to thermal expansion and contraction.
6.What mechanical and industrial applications can diaphragms be used in?
1. Pumps: Diaphragms are used in pumps to separate the pump chamber from the motor, allowing the pump to move fluid without the motor becoming contaminated.
2. Valves: Diaphragms are used in valves to control the flow of liquids and gases.
3. Compressors: Diaphragms are used in compressors to create a seal between the compressor and the cylinder, allowing the compressor to compress the air or gas.
4. Actuators: Diaphragms are used in actuators to convert energy into motion.
5. Filters: Diaphragms are used in filters to separate particles from liquids and gases.
6. Seals: Diaphragms are used in seals to create a tight seal between two surfaces.
7. Pressure Vessels: Diaphragms are used in pressure vessels to contain and control the pressure of a gas or liquid.
8. Heat Exchangers: Diaphragms are used in heat exchangers to separate two fluids while allowing heat to transfer between them.
7.What are the considerations for choosing between elastomeric diaphragms and non-elastomeric diaphragms for specific applications?
1. Cost: Elastomeric diaphragms are typically more expensive than non-elastomeric diaphragms.
2. Durability: Elastomeric diaphragms are more durable and can withstand higher pressures and temperatures than non-elastomeric diaphragms.
3. Chemical Compatibility: Elastomeric diaphragms are more resistant to chemical attack than non-elastomeric diaphragms.
4. Flexibility: Elastomeric diaphragms are more flexible than non-elastomeric diaphragms, allowing them to be used in applications where a tight seal is required.
5. Performance: Elastomeric diaphragms are better at maintaining a seal over time than non-elastomeric diaphragms.
8.Are diaphragms suitable for use in applications involving harsh radiation or extreme pressure differentials?
No, diaphragms are not suitable for use in applications involving harsh radiation or extreme pressure differentials. Diaphragms are designed to be used in applications with relatively low pressure differentials and are not designed to withstand extreme temperatures or radiation.
9.Are there diaphragms equipped with built-in sensors for real-time monitoring and feedback in automated systems?
Yes, there are diaphragms equipped with built-in sensors for real-time monitoring and feedback in automated systems. These diaphragms are typically used in industrial applications such as pumps, valves, and compressors. The sensors measure the pressure and flow of the system and provide feedback to the control system to ensure the system is operating correctly.
10.Are there diaphragms designed for pulsation dampening or shock absorption in hydraulic systems?
Yes, there are diaphragms designed for pulsation dampening and shock absorption in hydraulic systems. These diaphragms are typically made of rubber or elastomeric materials and are designed to absorb the shock and vibration of the hydraulic system. They are often used in applications such as hydraulic cylinders, pumps, and valves.
11.How do diaphragm rubber respond to cyclic or pulsating pressure loads, and what is their fatigue life in such conditions?
diaphragm rubber respond to cyclic or pulsating pressure loads by flexing and deflecting in response to the pressure. The fatigue life of a diaphragm in such conditions depends on the material used, the frequency of the pressure load, and the magnitude of the pressure load. Generally, fatigue life is shorter for higher frequency and higher magnitude pressure loads.