GENERAL SEALTECH LIMITED is a high-quality diaphragm product manufacturer that provides comprehensive services and has been meeting the diverse needs of many customers for over 20 years. We produce high-quality diaphragm products to meet your batch and customization needs. Our tradition is to maintain the shortest turnaround time in the industry, making us your reliable diaphragm production partner. Our engineers check the specified quality through tolerances on dimensions and required performance of the finished product to ensure timely delivery. Provide high-quality products at competitive prices and deliver them on time.
rubber diaphragm for air compressor technology can be widely used in various application fields. It can be used for material control and purification of liquids, steam, air, food, drugs, and other media, as well as isolation, catalysis, and membrane functions.
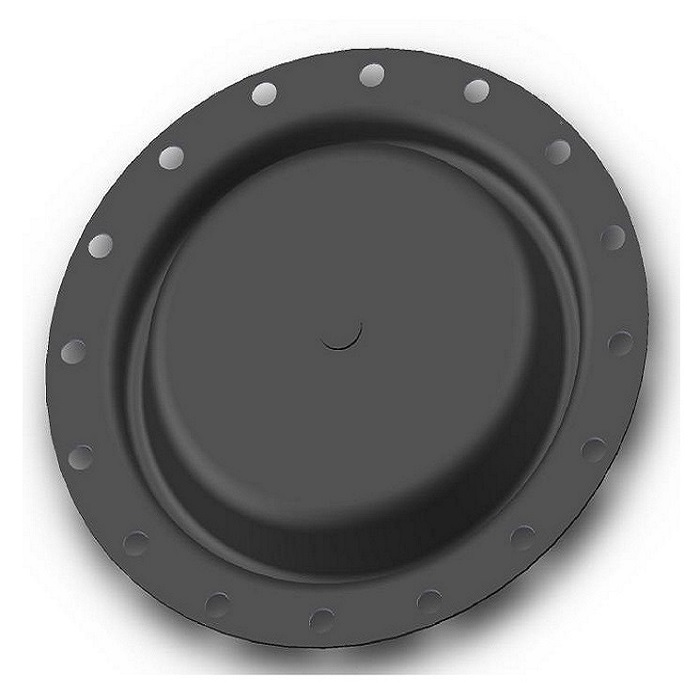
rubber diaphragm for air compressor is a universal and flexible sealing component that can provide variable sealing in flow control applications. The rubber diaphragms produced by GENERAL SEALTECH LIMITED are made of various single and composite elastomers, suitable for various industry applications.
The diaphragm is considered the most valuable component to meet all sealing needs, and our diaphragm seals are produced to adapt to any challenging shape and configuration, depending on your application requirements.
rubber diaphragm for air compressor is a flexible diaphragm, sometimes reinforced with fabric, strategically placed to prevent unnecessary transfer of material between two places by forming a seal. They can be used to separate two gases, two liquids, or one gas and one liquid that should not be mixed.
In fact, diaphragms come in various shapes and sizes. The thickness depends on the diameter and flexibility of the diaphragm
Membranes can be made of various materials, depending on the final application. Diaphragms have a wide range of applications, but are most commonly used in environments with pressure differences. The diaphragm has low fluid permeability and the ability to bend left and right, making it a sealing solution while providing consistent pressure difference.
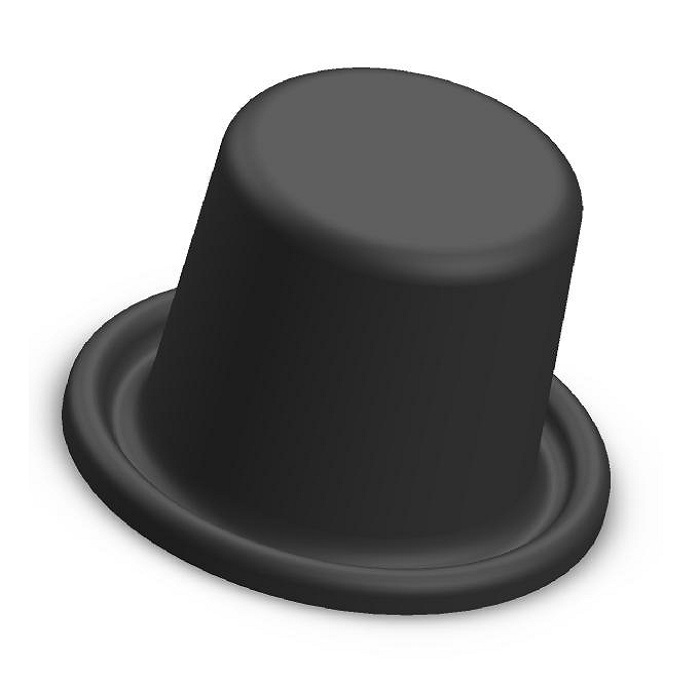
Why choose us?
- 1We manufacture Rubber diaphragms, Rolling diaphragms, LPG CNG Diaphragms, Teflon/PTFE Diaphragms, Solenoid Pulse Valve Diaphragms, Turbo Actuator Waste gate Diaphragms, Diaphragm Valve pump Diaphragms, Gas meter Diaphragms, etc.
rubber diaphragm for air compressor–A Guide to Frequently Asked Questions
2.Can diaphragms be used in applications requiring compliance with industry standards, such as FDA, ASME, or ISO?
3.Can diaphragms be customized for specific applications?
4.Are there specialized diaphragms for high-pressure applications, and what features make them suitable for these conditions?
5.What role do rubber diaphragm for air compressor play in controlling fluid flow and preventing leaks in pumps and valves?
6.What is a diaphragm?
7.What mechanical and industrial applications can diaphragms be used in?
8.Are there diaphragms designed for quick and easy replacement to minimize downtime in industrial processes?
9.What types of sealing mechanisms are commonly used with diaphragms, such as clamped, bolted, or adhesive seals?
1.How does the thickness of a diaphragm affect its flexibility and pressure resistance?
The thicker the diaphragm, the less flexible it will be and the more pressure it will be able to resist. This is because thicker diaphragms are more rigid and can withstand higher pressures without deforming. Thinner diaphragms are more flexible and can deform more easily under pressure, but they are also less resistant to pressure.
2.Can diaphragms be used in applications requiring compliance with industry standards, such as FDA, ASME, or ISO?
Yes, diaphragms can be used in applications requiring compliance with industry standards, such as FDA, ASME, or ISO. However, the specific requirements of the application must be taken into consideration when selecting the appropriate diaphragm material and design.
3.Can diaphragms be customized for specific applications?
Yes, diaphragms can be customized for specific applications. Depending on the application, the diaphragm can be made from different materials, such as rubber, plastic, or metal, and can be designed to meet specific requirements.
4.Are there specialized diaphragms for high-pressure applications, and what features make them suitable for these conditions?
Yes, there are specialized diaphragms for high-pressure applications. These diaphragms are designed to withstand higher pressures and temperatures than standard diaphragms. They are typically made from reinforced elastomers or metal materials such as stainless steel or Hastelloy. These materials are chosen for their strength and durability, as well as their ability to resist corrosion and wear. Additionally, these diaphragms are designed with thicker walls and reinforced edges to provide additional strength and stability.
5.What role do rubber diaphragm for air compressor play in controlling fluid flow and preventing leaks in pumps and valves?
rubber diaphragm for air compressor are flexible membranes that are used to control fluid flow and prevent leaks in pumps and valves. They are typically made of rubber or plastic and are designed to flex and move in response to pressure changes. When pressure is applied to one side of the diaphragm, it flexes and creates a seal that prevents fluid from leaking out. This seal is maintained until the pressure is released, allowing the diaphragm to return to its original shape and allowing the fluid to flow freely. Diaphragms are used in a variety of applications, including pumps, valves, and other fluid control systems.
6.What is a diaphragm?
A diaphragm is a thin, dome-shaped muscle located between the thoracic and abdominal cavities. It is the primary muscle of respiration and helps to regulate the flow of air into and out of the lungs. The diaphragm also plays an important role in aiding digestion by helping to move food through the digestive tract.
7.What mechanical and industrial applications can diaphragms be used in?
1. Pumps: Diaphragms are used in pumps to separate the pump chamber from the motor, allowing the pump to move fluid without the motor becoming contaminated.
2. Valves: Diaphragms are used in valves to control the flow of liquids and gases.
3. Compressors: Diaphragms are used in compressors to create a seal between the compressor and the cylinder, allowing the compressor to compress the air or gas.
4. Actuators: Diaphragms are used in actuators to convert energy into motion.
5. Filters: Diaphragms are used in filters to separate particles from liquids and gases.
6. Seals: Diaphragms are used in seals to create a tight seal between two surfaces.
7. Pressure Vessels: Diaphragms are used in pressure vessels to contain and control the pressure of a gas or liquid.
8. Heat Exchangers: Diaphragms are used in heat exchangers to separate two fluids while allowing heat to transfer between them.
8.Are there diaphragms designed for quick and easy replacement to minimize downtime in industrial processes?
Yes, there are diaphragms designed for quick and easy replacement to minimize downtime in industrial processes. These diaphragms are typically made of materials such as rubber, silicone, or PTFE, and are designed to be easily replaced without the need for tools or special equipment. Additionally, some diaphragms are designed with quick-connect fittings to further reduce downtime.
9.What types of sealing mechanisms are commonly used with diaphragms, such as clamped, bolted, or adhesive seals?
1. Clamped Seals: Clamped seals are the most common type of diaphragm seal. They are typically used in applications where the pressure is relatively low and the temperature is not too extreme. Clamped seals are easy to install and provide a reliable seal.
2. Bolted Seals: Bolted seals are used in applications where the pressure is higher and the temperature is more extreme. They are more difficult to install than clamped seals, but provide a more reliable seal.
3. Adhesive Seals: Adhesive seals are used in applications where the pressure is low and the temperature is not too extreme. They are easy to install and provide a reliable seal. However, they are not as reliable as clamped or bolted seals.
Products Tags: Teflon/PTFE diaphragm