We started producing diaphragms in 1990 and entered the international market in 2007. We have been committed to diaphragm technology, and finally overcome some difficult products.
GENERAL SEALTECH LIMITED is a diaphragm supplier with 23 years of film production experience. The main products are Rubber diaphragms, Rolling diaphragms, LPG CNG Diaphragms, Teflon/PTFE Diaphragms, Solenoid Pulse Valve Diaphragms, Turbo Actuator Waste gate Diaphragms, Diaphragm Valve pump Diaphragms, Gas meter Diaphragms, etc.
Another advantage of separators is that they can provide a certain degree of protection to prevent cross contamination of substances, which is particularly important for fields such as laboratories, food, environment, healthcare, and metallurgy.
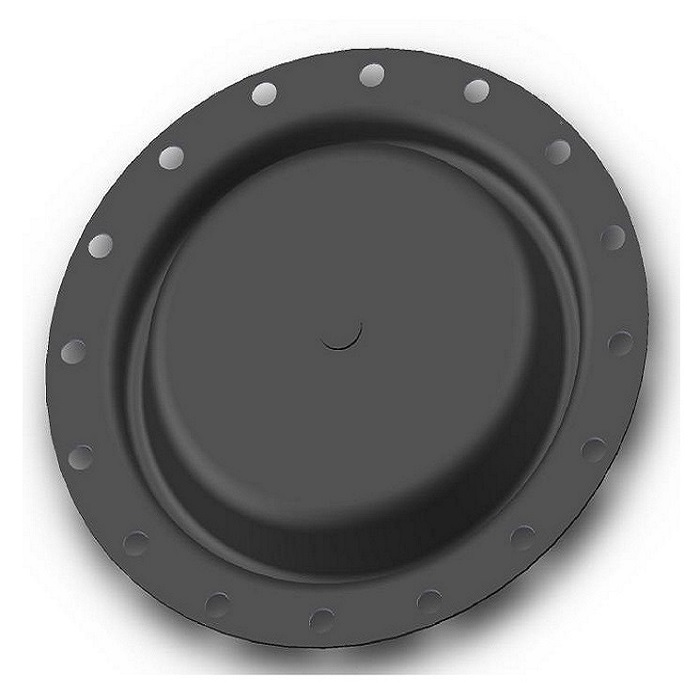
Diaphragm rubber seal is a universal and flexible sealing component that can provide variable sealing in flow control applications. The rubber diaphragms produced by GENERAL SEALTECH LIMITED are made of various single and composite elastomers, suitable for various industry applications.
The diaphragm is considered the most valuable component to meet all sealing needs, and our diaphragm seals are produced to adapt to any challenging shape and configuration, depending on your application requirements.
Diaphragm rubber seal is a flexible diaphragm, sometimes reinforced with fabric, strategically placed to prevent unnecessary transfer of material between two places by forming a seal. They can be used to separate two gases, two liquids, or one gas and one liquid that should not be mixed.
In fact, diaphragms come in various shapes and sizes. The thickness depends on the diameter and flexibility of the diaphragm
Membranes can be made of various materials, depending on the final application. Diaphragms have a wide range of applications, but are most commonly used in environments with pressure differences. The diaphragm has low fluid permeability and the ability to bend left and right, making it a sealing solution while providing consistent pressure difference.
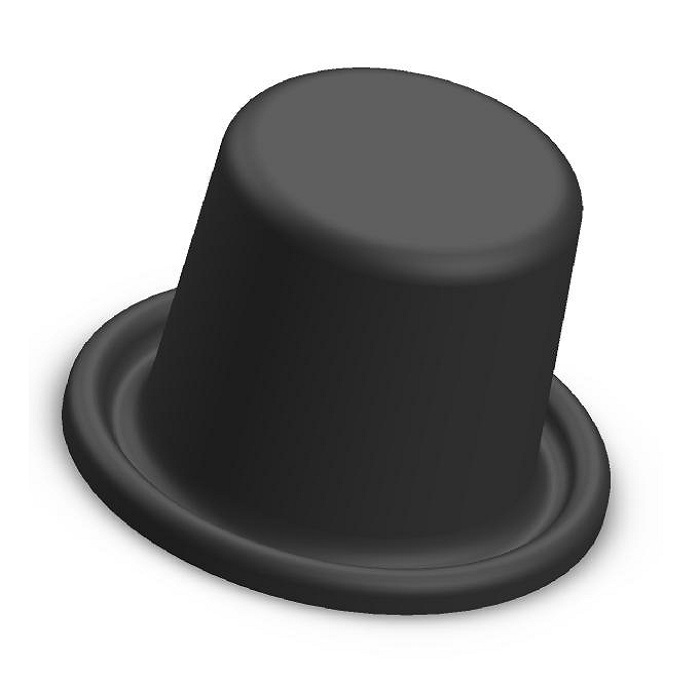
Why choose us?
- 11. We have more than 15 years of industry experience in water treatment.2. High quality products and competitive price.3. We have professional business personnel and engineers to provide you with type selection assistance and technical support.
Diaphragm rubber seal–A Guide to Frequently Asked Questions
2.Do diaphragm rubber seal have electrical conductivity properties, and can they be used in applications requiring EMI/RFI shielding?
3.How do diaphragms perform in high-vibration environments, and what measures are taken to ensure their reliability in these conditions?
4.Are there diaphragms designed for use in critical industries such as aerospace and healthcare, and what unique properties do they possess?
5.Are there diaphragms equipped with built-in sensors for real-time monitoring and feedback in automated systems?
6.What types of testing and quality control measures are applied to ensure the reliability and performance of diaphragms?
7.How are diaphragms designed to resist abrasion and wear in applications with abrasive media?
8.Can diaphragms be used in applications requiring compliance with industry standards, such as FDA, ASME, or ISO?
9.What are the key characteristics that make diaphragms suitable for sealing and pressure regulation in different systems?
1.Are there diaphragms designed for quick and easy replacement to minimize downtime in industrial processes?
Yes, there are diaphragms designed for quick and easy replacement to minimize downtime in industrial processes. These diaphragms are typically made of materials such as rubber, silicone, or PTFE, and are designed to be easily replaced without the need for tools or special equipment. Additionally, some diaphragms are designed with quick-connect fittings to further reduce downtime.
2.Do diaphragm rubber seal have electrical conductivity properties, and can they be used in applications requiring EMI/RFI shielding?
No, diaphragm rubber seal do not have electrical conductivity properties and cannot be used in applications requiring EMI/RFI shielding. Diaphragms are typically made of rubber or plastic and are used to control the flow of air or other gases.
3.How do diaphragms perform in high-vibration environments, and what measures are taken to ensure their reliability in these conditions?
Diaphragms are designed to be highly reliable in high-vibration environments. To ensure their reliability, measures such as using thicker diaphragm material, using multiple layers of material, and using dampening materials such as rubber or foam are taken. Additionally, the diaphragm should be securely mounted to the structure to prevent it from vibrating excessively. Finally, the diaphragm should be inspected regularly to ensure that it is not damaged or worn out.
4.Are there diaphragms designed for use in critical industries such as aerospace and healthcare, and what unique properties do they possess?
Yes, there are diaphragms designed for use in critical industries such as aerospace and healthcare. These diaphragms are typically made from high-performance materials such as PTFE, FKM, and EPDM, which offer superior chemical and temperature resistance, as well as excellent durability and strength. Additionally, these diaphragms are designed to meet the stringent requirements of these industries, such as tight tolerances, high-pressure ratings, and low-leakage rates.
5.Are there diaphragms equipped with built-in sensors for real-time monitoring and feedback in automated systems?
Yes, there are diaphragms equipped with built-in sensors for real-time monitoring and feedback in automated systems. These diaphragms are typically used in industrial applications such as pumps, valves, and compressors. The sensors measure the pressure and flow of the system and provide feedback to the control system to ensure the system is operating correctly.
6.What types of testing and quality control measures are applied to ensure the reliability and performance of diaphragms?
1. Visual Inspection: Visual inspection is used to check for any visible defects in the diaphragm material, such as cracks, tears, or other damage.
2. Pressure Testing: Pressure testing is used to ensure that the diaphragm can withstand the pressure it is designed to handle.
3. Leak Testing: Leak testing is used to check for any leaks in the diaphragm material.
4. Durability Testing: Durability testing is used to ensure that the diaphragm can withstand the wear and tear of its intended use.
5. Chemical Testing: Chemical testing is used to check for any chemical reactions that could affect the performance of the diaphragm.
6. Electrical Testing: Electrical testing is used to check for any electrical issues that could affect the performance of the diaphragm.
7. Temperature Testing: Temperature testing is used to ensure that the diaphragm can withstand the temperatures it is designed to handle.
7.How are diaphragms designed to resist abrasion and wear in applications with abrasive media?
Diaphragms are designed to resist abrasion and wear in applications with abrasive media by using materials that are highly resistant to abrasion and wear. These materials include polyurethane, rubber, and other elastomers. The diaphragm is also designed with a thicker wall and reinforced edges to provide additional protection against abrasion and wear. Additionally, the diaphragm may be coated with a protective material such as a fluoropolymer to further reduce wear and tear.
8.Can diaphragms be used in applications requiring compliance with industry standards, such as FDA, ASME, or ISO?
Yes, diaphragms can be used in applications requiring compliance with industry standards, such as FDA, ASME, or ISO. However, the specific requirements of the application must be taken into consideration when selecting the appropriate diaphragm material and design.
9.What are the key characteristics that make diaphragms suitable for sealing and pressure regulation in different systems?
1. Flexibility: Diaphragms are flexible and can be designed to fit a variety of shapes and sizes. This allows them to be used in a wide range of applications.
2. Durability: Diaphragms are made from strong materials that can withstand high pressures and temperatures. This makes them suitable for use in high-pressure systems.
3. Low Maintenance: Diaphragms require minimal maintenance and can be easily replaced when needed.
4. Low Cost: Diaphragms are relatively inexpensive compared to other sealing and pressure regulation solutions.
5. Versatility: Diaphragms can be used in a variety of applications, from automotive to industrial.