What is a rubber diaphragm?
Rubber diaphragm is a flexible, usually circular diaphragm made of rubber or elastic material. Its design can respond to changes in pressure, allowing it to move and bend when subjected to different forces. Rubber diaphragms are commonly used in various applications, where controlled transmission of pressure, motion, or fluid is crucial.
Function:
Rubber diaphragms are mainly used to transmit or control the pressure difference between two areas. When pressure is applied to one side of the diaphragm, it will bend or deform, resulting in a corresponding reaction force on the other side. This deformation can be used for various purposes, such as actuating valves, controlling fluid flow, generating mechanical motion, or measuring pressure changes.
Materials:
Rubber diaphragm is usually made of elastomer materials, such as natural rubber, synthetic rubber (such as chloroprene rubber, silicone resin, or nitrile rubber), or thermoplastic elastomer (TPE). The selection of materials depends on the specific application requirements, including factors such as chemical compatibility, temperature resistance, and flexibility.
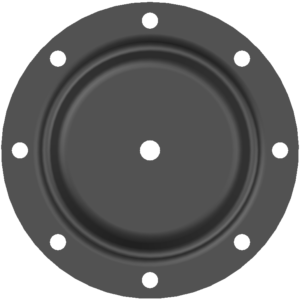
rubber diaphragm
Application and advantages of rubber diaphragm
Rubber diaphragms are widely used in various industries and equipment, including:
Automobile: used for carburetors, fuel pumps, EGR valves, and braking systems.
Industry: Used for pressure regulators, control valves, pumps, actuators, and sensors.
Medical: Used for various medical equipment, such as respirators, infusion pumps, and pressure sensitive devices.
Aerospace: Aircraft and spacecraft systems used to control fuel flow, pressure, and fluid movement.
Hydraulics: A hydraulic system used to control fluid pressure and motion.
Pneumatic: Pneumatic actuators and valves used to control air pressure and movement.
Flexibility: They can adapt to various pressures and respond to subtle changes.
Advantages:
Reliability: They can consistently function even in challenging environments.
Cost effectiveness: Rubber diaphragms are typically a cost-effective solution for pressure control applications.
Universality: They can be designed for specific pressure ranges and motion requirements.
How is rubber diaphragm produced?
The production of rubber diaphragm includes several manufacturing steps:
1. Material selection:
Select appropriate rubber materials for the diaphragm based on application requirements such as chemical compatibility, temperature resistance, and flexibility. Common rubber materials include natural rubber, chloroprene rubber, silicone resin, and nitrile rubber.
2. Mixing and preparation:
The selected rubber material is mixed and compounded with various additives, such as curing agents, accelerators, and fillers. This process ensures that the rubber has the required properties, such as elasticity, strength, and resistance to environmental factors.
3. Forming:
Then, using molding technology, the composite rubber material is formed into the desired diaphragm shape. There are various molding methods, including compression molding and injection molding.
4. Trimming and cutting:
After the diaphragm is formed, it is usually taken out of the mold and trimmed and cut to obtain the final required size and shape. Remove excess rubber material and address any defects.
5. Quality control:
Throughout the entire production process, quality control measures were implemented to ensure that the diaphragm meets the specified standards. This may involve visual inspection, measurement, and testing of characteristics such as elasticity, thickness, and pressure response.
6. Maintenance:
Once the membranes are formed and trimmed, they undergo a curing process to achieve their final mechanical properties. Curing involves exposing the membrane to heat and pressure for a specific period of time to promote cross-linking of rubber molecules and improve their strength and durability.
7. Post curing and surface treatment:
After curing, the membrane may undergo additional post curing processes to ensure complete curing and stability of its performance. Depending on the application, surface treatment or finishing steps such as coatings may be used to enhance resistance to specific environments or substances.
8. Inspection and Packaging:
Each diaphragm must undergo a final inspection to ensure that its quality and performance meet the required standards. Once approved, the diaphragms are packaged and ready to be distributed to manufacturers and industries that use them in various applications.
How to choose the high-quality rubber diaphragm manufacturers for procurement?
1. Research and shortlisted:
Start by researching potential rubber diaphragm manufacturers. Looking for manufacturers with good reputation, industry experience, and a record of producing high-quality products. You can search online, seek recommendations from industry peers, or consult industry associations.
2. Quality standards and certification:
Check if the manufacturer complies with industry quality standards and certifications. ISO certification, such as ISO 9001, indicates that the manufacturer follows a strict quality control process. Ensure that their products meet the regulatory standards required by your industry.
3. Manufacturing capacity:
Evaluate the manufacturer’s manufacturing capabilities. Do they have advanced molding and curing equipment? Do they provide customized options to meet your specific needs? Manufacturers with modern equipment and skilled technical personnel are more likely to produce high-quality diaphragms.
4. Material expertise:
Ask them about the range of rubber materials they use and their professional knowledge in these materials. Different applications require different rubber compounds with specific properties. Understanding the manufacturers of rubber materials can provide the right choices for your application.
5. Testing and Quality Control:
Ask the manufacturer about their testing and quality control processes. Do they thoroughly inspect and test each diaphragm to ensure compliance with specifications? Manufacturers investing in quality control are more likely to provide consistent and reliable products.
6. Customization and Support:
If your application requires customized diaphragms, please ensure that the manufacturer can provide design and engineering support. A manufacturer willing to collaborate on design and provide technical assistance demonstrates their commitment to meeting your specific requirements.
8. Production capacity and delivery cycle:
Consider the manufacturer’s production capacity and lead time. Can they meet your order quantity and delivery deadline without affecting quality? Timely delivery is crucial for your operations.
What production equipment do rubber diaphragm manufacturers need?
1. Mixing and preparation equipment:
Banbury mixer: used to mix rubber materials with additives to produce the desired rubber compound.
2. Forming equipment:
Compression molding machine: used to shape and solidify rubber materials into membranes under heat and pressure.
Injection molding machine: used to inject molten rubber into the mold cavity, producing rubber membranes with complex shapes.
3. Cutting and trimming equipment:
Die cutting machine: used to cut and trim rubber membranes into the required size and shape.
Water jet cutting system: used to accurately cut rubber materials using high-pressure water jet.
4. Maintenance equipment:
Autoclave: A high-pressure vessel used to solidify rubber membranes under controlled temperature and pressure conditions.
5. Testing and Inspection Equipment:
Tensile testing machine: measures the tensile strength and elasticity of rubber membranes.
Hardness tester: measures the hardness of rubber materials.
Optical testing equipment: used for visual inspection of the surface quality and size of the membrane.
Pressure testing equipment: tests the pressure resistance and integrity of the diaphragm.
6. Post curing and surface treatment equipment:
Post curing furnace: used for additional curing of membranes to improve their mechanical properties.
Surface treatment equipment: Apply coatings or treatments to enhance the resistance of the diaphragm to chemicals, wear, or other factors.
7. Mixing and dispensing equipment:
Dispensing system: used to accurately distribute rubber compounds and additives during the mixing process.
8. Material handling equipment:
Conveyors and material handling systems: Transport raw materials and finished diaphragms between different production stages.
9. Computer Aided Design (CAD) and Manufacturing (CAM) Software:
Used for designing diaphragm molds, developing production plans, and optimizing manufacturing processes.
10. Quality control equipment:
Size measuring tools: calipers, micrometers, and other tools used to accurately measure the size of the diaphragm.
Visual inspection tools: magnifying glass, microscope, and camera, used for detailed visual inspection.
Service and Quality System of Rubber Diaphragm Manufacturers
Rubber diaphragm manufacturers are committed to providing the highest quality products and services, which requires a strict quality system. The quality system specifies the necessary resources and processes in place to ensure the quality of each diaphragm order.
Quality laboratory: The laboratory should include all necessary instruments and equipment to inspect and test diaphragm materials and ensure that the products comply with the manufacturer’s standards.
Document Control/Document System: Training and customer feedback will specify what documents are required for each diaphragm order. The documented quality system should include policies and procedures, as well as records and reports, to establish traceability and accountability for each product.
Manufacturing process: Established guidelines should be followed to improve the efficiency of diaphragm order production and maintain consistency. These processes should be continuously evaluated and updated as needed.
Quality inspection: Experienced and well-trained personnel should be equipped to inspect the diaphragm for any defects or signs of defects. Inspection can include visual inspection, dimensional inspection, hardness testing, and burst testing to ensure that the product meets the requirements of the manufacturer and customer.
Continuous improvement: Priority should be given to continuous improvement to ensure that all diaphragm orders meet the highest standards. All personnel should receive continuous training and evaluation to ensure that they are able to effectively interpret and use the quality system.
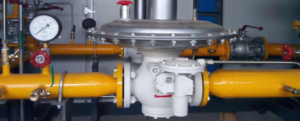
Rubber diaphragm
What is a rubber diaphragm design?
Rubber diaphragm design refers to the process of developing a detailed plan or blueprint for the construction of rubber diaphragms. The design includes multiple aspects, including the shape, size, thickness, material selection, reinforcement, and other functions of the diaphragm.
1. Application requirements:
Understand the specific applications that the diaphragm will be used for. Consider factors such as pressure range, temperature, chemical compatibility, and the type of fluid or gas that the diaphragm will come into contact with.
2. Material selection:
Select appropriate rubber materials according to application requirements. Consider factors such as elasticity, durability, chemical resistance, and temperature resistance. Different rubber compounds have different properties and are suitable for different environments.
3. Shape and size:
Determine the optimal shape and size of the diaphragm based on its expected function and installation equipment. Consider factors such as space limitations, flow requirements, and pressure distribution.
4. Thickness and reinforcement:
Determine the thickness of the diaphragm considering the required flexibility and strength. In some cases, adding reinforcement layers such as fabric or mesh can enhance the mechanical properties of the diaphragm.
5. Pressure and flow analysis:
Analyze the pressure difference and fluid flow conditions that the diaphragm will face. Ensure that the diaphragm can handle these conditions without deformation or failure.
6. Accessories and Seals:
Plan the connection and sealing method of the diaphragm inside the equipment. This includes designing functions such as flanges, grommets, or seals to prevent leakage and ensure secure installation.
7. Flexibility and driving force:
Consider the reaction of the diaphragm to pressure changes. The flexibility of the diaphragm and its ability to accurately transmit pressure changes are crucial for its performance.
8. Durability and lifespan:
The design of the diaphragm should be able to withstand the expected wear and tear of its operating environment. This includes considering factors such as wear, fatigue, and exposure to chemicals.
9. Testing and Verification:
Plan testing and validation procedures to ensure that the designed diaphragm meets its expected performance standards. This may involve pressure testing, durability testing, and material compatibility testing.