We are engaged in the research, development, production, process, marketing and trade of diaphragms. We have experienced and professional staff members. We have strong mold development capabilities and high precision instruments and equipment. We specialize in the production of Rubber diaphragms, Rolling diaphragms, LPG CNG Diaphragms, Teflon/PTFE Diaphragms,etc.After more than 15 years of pioneering venture, we have already become a professional company in the field. We follow the “leading technology, improving quality” principle. Our products are exported to Europe, America and Southeast Asia.
Air compressor rubber diaphragm products typically have high plasticity and can be used in very low temperatures and high temperature ranges. They can also be produced using different technologies such as thin film construction, hot melt construction, and fiber construction.
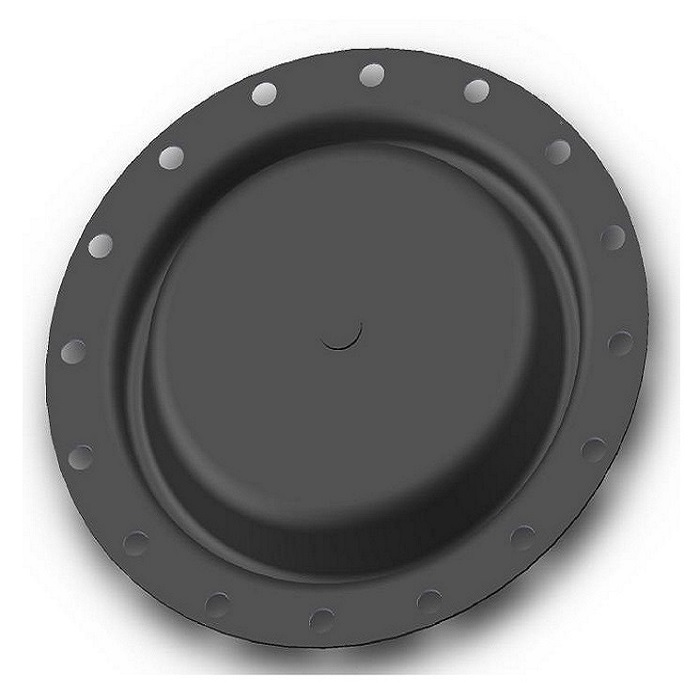
Air compressor rubber diaphragm is a universal and flexible sealing component that can provide variable sealing in flow control applications. The rubber diaphragms produced by GENERAL SEALTECH LIMITED are made of various single and composite elastomers, suitable for various industry applications.
The diaphragm is considered the most valuable component to meet all sealing needs, and our diaphragm seals are produced to adapt to any challenging shape and configuration, depending on your application requirements.
Air compressor rubber diaphragm is a flexible diaphragm, sometimes reinforced with fabric, strategically placed to prevent unnecessary transfer of material between two places by forming a seal. They can be used to separate two gases, two liquids, or one gas and one liquid that should not be mixed.
In fact, diaphragms come in various shapes and sizes. The thickness depends on the diameter and flexibility of the diaphragm
Membranes can be made of various materials, depending on the final application. Diaphragms have a wide range of applications, but are most commonly used in environments with pressure differences. The diaphragm has low fluid permeability and the ability to bend left and right, making it a sealing solution while providing consistent pressure difference.
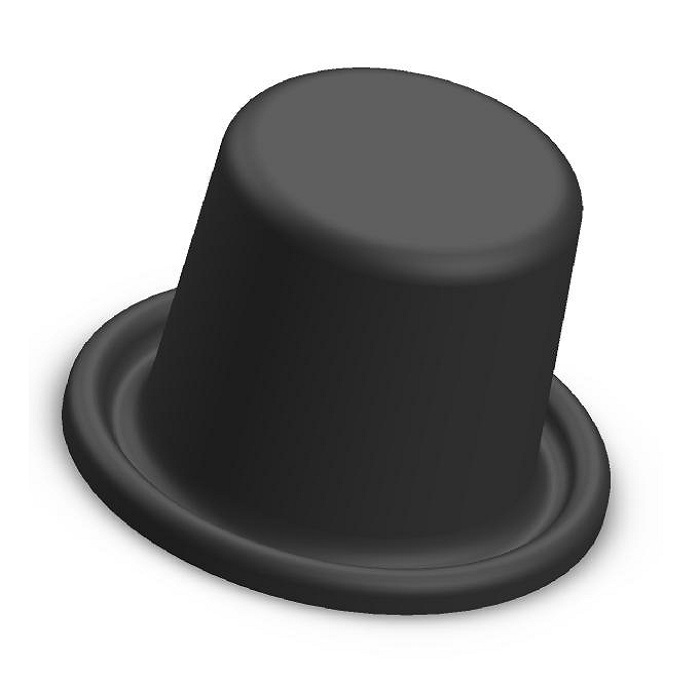
Why choose us?
We manufacture Rubber diaphragms, Rolling diaphragms, LPG CNG Diaphragms, Teflon/PTFE Diaphragms, Solenoid Pulse Valve Diaphragms, Turbo Actuator Waste gate Diaphragms, Diaphragm Valve pump Diaphragms, Gas meter Diaphragms, etc.
Air compressor rubber diaphragm–A Guide to Frequently Asked Questions
2.Are there diaphragms designed for pulsation dampening or shock absorption in hydraulic systems?
3.What is the role of diaphragms in controlling the flow of aggressive or corrosive chemicals in chemical processing applications?
4.Can diaphragms be used in contact with food or pharmaceutical products, and what certifications are required for compliance with industry standards?
5.What are the key characteristics that make diaphragms suitable for sealing and pressure regulation in different systems?
6.What innovations and advancements have been made in diaphragm technology in recent years?
7.Can diaphragms be used in applications requiring compliance with industry standards, such as FDA, ASME, or ISO?
8.Can diaphragms be used in both dynamic and static sealing applications, and what are the differences in their design and performance?
9.Are there diaphragms designed for use in critical industries such as aerospace and healthcare, and what unique properties do they possess?
10.Are there diaphragms equipped with built-in sensors for real-time monitoring and feedback in automated systems?
11.Are diaphragms suitable for use in applications involving harsh radiation or extreme pressure differentials?
1.How do air compressor rubber diaphragm contribute to the isolation of different process media or gases within a system?
air compressor rubber diaphragm are used to separate different process media or gases within a system by creating a physical barrier between them. This barrier prevents the media or gases from mixing, thus providing a degree of isolation. Diaphragms are also used to control the flow of media or gases within a system, as they can be designed to open and close in response to pressure or other external factors.
2.Are there diaphragms designed for pulsation dampening or shock absorption in hydraulic systems?
Yes, there are diaphragms designed for pulsation dampening and shock absorption in hydraulic systems. These diaphragms are typically made of rubber or elastomeric materials and are designed to absorb the shock and vibration of the hydraulic system. They are often used in applications such as hydraulic cylinders, pumps, and valves.
3.What is the role of diaphragms in controlling the flow of aggressive or corrosive chemicals in chemical processing applications?
Diaphragms are used to control the flow of aggressive or corrosive chemicals in chemical processing applications. They act as a barrier between the chemical and the process equipment, preventing the chemical from coming into contact with the equipment and causing corrosion or other damage. Diaphragms are also used to regulate the flow of the chemical, allowing for precise control of the process.
4.Can diaphragms be used in contact with food or pharmaceutical products, and what certifications are required for compliance with industry standards?
Yes, diaphragms can be used in contact with food or pharmaceutical products. Depending on the application, the diaphragm must meet certain industry standards and certifications. For food contact applications, the diaphragm must meet the requirements of the US Food and Drug Administration (FDA) and the European Union (EU) Regulation 10/2011. For pharmaceutical applications, the diaphragm must meet the requirements of the US Pharmacopeia (USP) Class VI and the European Pharmacopoeia (EP).
5.What are the key characteristics that make diaphragms suitable for sealing and pressure regulation in different systems?
1. Flexibility: Diaphragms are flexible and can be designed to fit a variety of shapes and sizes. This allows them to be used in a wide range of applications.
2. Durability: Diaphragms are made from strong materials that can withstand high pressures and temperatures. This makes them suitable for use in high-pressure systems.
3. Low Maintenance: Diaphragms require minimal maintenance and can be easily replaced when needed.
4. Low Cost: Diaphragms are relatively inexpensive compared to other sealing and pressure regulation solutions.
5. Versatility: Diaphragms can be used in a variety of applications, from automotive to industrial.
6.What innovations and advancements have been made in diaphragm technology in recent years?
1. Improved materials: Diaphragms are now made from a variety of materials, including polyurethane, silicone, and other elastomers. These materials are more durable and provide better performance than traditional materials.
2. Improved design: Diaphragms are now designed with more precise tolerances and better sealing capabilities. This allows for better performance and longer life.
3. Improved manufacturing processes: Advances in manufacturing processes have allowed for more efficient production of diaphragms, resulting in lower costs and improved quality.
4. Improved sensing capabilities: Diaphragms are now able to sense pressure, temperature, and other variables, allowing for more accurate control of systems.
5. Improved control systems: Diaphragms are now used in a variety of control systems, including valves, pumps, and other devices. This allows for better control and more efficient operation.
7.Can diaphragms be used in applications requiring compliance with industry standards, such as FDA, ASME, or ISO?
Yes, diaphragms can be used in applications requiring compliance with industry standards, such as FDA, ASME, or ISO. However, the specific requirements of the application must be taken into consideration when selecting the appropriate diaphragm material and design.
8.Can diaphragms be used in both dynamic and static sealing applications, and what are the differences in their design and performance?
Yes, diaphragms can be used in both dynamic and static sealing applications. The main difference between the two is in the design and performance.
Dynamic sealing applications require a diaphragm that is designed to withstand the constant movement and pressure of the application. This type of diaphragm is usually made of a flexible material such as rubber or silicone, and is designed to flex and move with the application.
Static sealing applications require a diaphragm that is designed to remain in a fixed position and provide a tight seal. This type of diaphragm is usually made of a rigid material such as metal or plastic, and is designed to remain in a fixed position and provide a tight seal.
9.Are there diaphragms designed for use in critical industries such as aerospace and healthcare, and what unique properties do they possess?
Yes, there are diaphragms designed for use in critical industries such as aerospace and healthcare. These diaphragms are typically made from high-performance materials such as PTFE, FKM, and EPDM, which offer superior chemical and temperature resistance, as well as excellent durability and strength. Additionally, these diaphragms are designed to meet the stringent requirements of these industries, such as tight tolerances, high-pressure ratings, and low-leakage rates.
10.Are there diaphragms equipped with built-in sensors for real-time monitoring and feedback in automated systems?
Yes, there are diaphragms equipped with built-in sensors for real-time monitoring and feedback in automated systems. These diaphragms are typically used in industrial applications such as pumps, valves, and compressors. The sensors measure the pressure and flow of the system and provide feedback to the control system to ensure the system is operating correctly.
11.Are diaphragms suitable for use in applications involving harsh radiation or extreme pressure differentials?
No, diaphragms are not suitable for use in applications involving harsh radiation or extreme pressure differentials. Diaphragms are designed to be used in applications with relatively low pressure differentials and are not designed to withstand extreme temperatures or radiation.
Tags: rubber diaphragm , rolling diaphragm