Our company’s excellent reputation is built on our ability to provide the most effective manufacturing solutions to meet the most demanding applications of our esteemed customers. Our main goal is to continuously exceed customer expectations, providing them with high-performance diaphragm products, competitive prices, on-time delivery, and excellent customer service. GENERAL SEALTECH LIMITED is committed to always meeting all of your blueprint specifications and tolerance requirements.
We specialize in producing various types of diaphragm products, including rubber diaphragms and rolling diaphragms, among others.
The design principle of a diaphragm is to use the failure strength and failure mode of materials or structures to set personalized control strategies for a certain heat or mass transfer medium, or for the occurrence of certain flow or diffusion effects, in order to achieve specific functions or protocols.
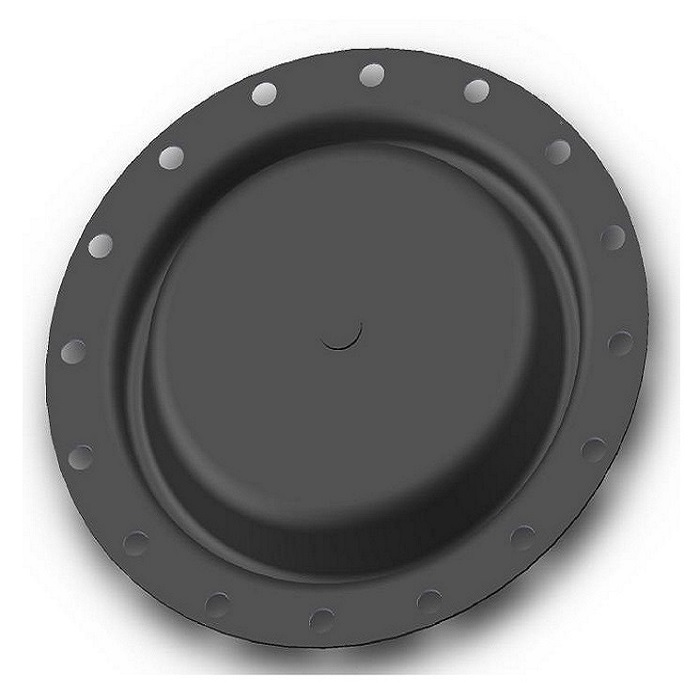
air brake rubber diaphragm is a universal and flexible sealing component that can provide variable sealing in flow control applications. The rubber diaphragms produced by GENERAL SEALTECH LIMITED are made of various single and composite elastomers, suitable for various industry applications.
The diaphragm is considered the most valuable component to meet all sealing needs, and our diaphragm seals are produced to adapt to any challenging shape and configuration, depending on your application requirements.
air brake rubber diaphragm is a flexible diaphragm, sometimes reinforced with fabric, strategically placed to prevent unnecessary transfer of material between two places by forming a seal. They can be used to separate two gases, two liquids, or one gas and one liquid that should not be mixed.
In fact, diaphragms come in various shapes and sizes. The thickness depends on the diameter and flexibility of the diaphragm
Membranes can be made of various materials, depending on the final application. Diaphragms have a wide range of applications, but are most commonly used in environments with pressure differences. The diaphragm has low fluid permeability and the ability to bend left and right, making it a sealing solution while providing consistent pressure difference.
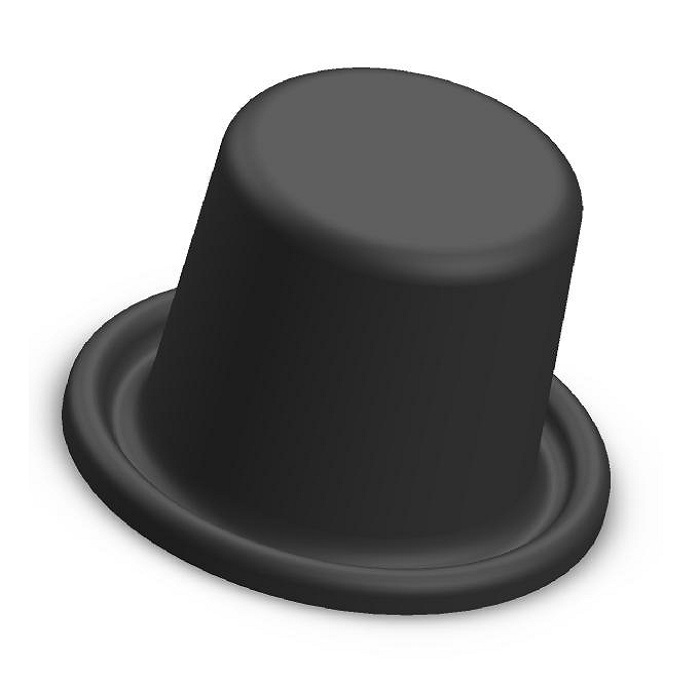
Why choose us?
- 1We manufacture Rubber diaphragms, Rolling diaphragms, LPG CNG Diaphragms, Teflon/PTFE Diaphragms, Solenoid Pulse Valve Diaphragms, Turbo Actuator Waste gate Diaphragms, Diaphragm Valve pump Diaphragms, Gas meter Diaphragms, etc.
# | air brake rubber diaphragm Parameter | Information |
---|---|---|
1 | Place of Origin | China |
2 | Brand Name | GENERAL SEALTECH LIMITED |
3 | working temperature | -200℃~+250℃ |
4 | Color | Any |
5 | Certificate | Ce |
6 | OEM | Yes |
7 | Packaging | Carton |
air brake rubber diaphragm–A Guide to Frequently Asked Questions
2.How do diaphragms perform in high-vibration environments, and what measures are taken to ensure their reliability in these conditions?
3.Can diaphragms be used in applications requiring compliance with industry standards, such as FDA, ASME, or ISO?
4.Are there diaphragms equipped with built-in sensors for real-time monitoring and feedback in automated systems?
5.How do diaphragms perform in vacuum applications, and are there special considerations for these conditions?
6.Are diaphragms used in safety relief valves and pressure relief devices to prevent overpressure situations?
7.What are the considerations for choosing between elastomeric diaphragms and non-elastomeric diaphragms for specific applications?
8.How are diaphragms designed to resist chemical corrosion and degradation in aggressive environments?
9.How do diaphragms provide sealing solutions in hydraulic accumulators and fluid reservoirs?
10.Are there specialized diaphragms for high-pressure applications, and what features make them suitable for these conditions?
11.How do diaphragms maintain their flexibility and resilience over time, and what factors can lead to wear or degradation?
12.Can diaphragms be used in contact with food or pharmaceutical products, and what certifications are required for compliance with industry standards?
13.Are there diaphragms made from eco-friendly or sustainable materials for environmentally conscious applications?
14.Can diaphragms be used in medical devices, and what biocompatibility standards do they need to meet?
15.Are there diaphragms designed for pulsation dampening or shock absorption in hydraulic systems?
1.How do diaphragms contribute to the precision and accuracy of pressure control and regulation systems?
Diaphragms are used in pressure control and regulation systems to provide a precise and accurate control of pressure. They are used to separate the pressure sensing element from the process fluid, allowing for a more accurate and repeatable measurement of pressure. The diaphragm also acts as a barrier to prevent contamination of the sensing element, which can lead to inaccurate readings. The diaphragm also helps to dampen pressure fluctuations, providing a more stable and consistent pressure control.
2.How do diaphragms perform in high-vibration environments, and what measures are taken to ensure their reliability in these conditions?
Diaphragms are designed to be highly reliable in high-vibration environments. To ensure their reliability, measures such as using thicker diaphragm material, using multiple layers of material, and using dampening materials such as rubber or foam are taken. Additionally, the diaphragm should be securely mounted to the structure to prevent it from vibrating excessively. Finally, the diaphragm should be inspected regularly to ensure that it is not damaged or worn out.
3.Can diaphragms be used in applications requiring compliance with industry standards, such as FDA, ASME, or ISO?
Yes, diaphragms can be used in applications requiring compliance with industry standards, such as FDA, ASME, or ISO. However, the specific requirements of the application must be taken into consideration when selecting the appropriate diaphragm material and design.
4.Are there diaphragms equipped with built-in sensors for real-time monitoring and feedback in automated systems?
Yes, there are diaphragms equipped with built-in sensors for real-time monitoring and feedback in automated systems. These diaphragms are typically used in industrial applications such as pumps, valves, and compressors. The sensors measure the pressure and flow of the system and provide feedback to the control system to ensure the system is operating correctly.
5.How do diaphragms perform in vacuum applications, and are there special considerations for these conditions?
Diaphragms are commonly used in vacuum applications to control the flow of air or other gases. They are designed to be flexible and resilient, allowing them to maintain a seal even when exposed to low pressure. Special considerations for vacuum applications include the use of materials that are resistant to corrosion and abrasion, as well as the use of a diaphragm with a larger surface area to ensure a better seal. Additionally, the diaphragm should be designed to withstand the extreme temperatures and pressures associated with vacuum applications.
6.Are diaphragms used in safety relief valves and pressure relief devices to prevent overpressure situations?
Yes, diaphragms are commonly used in safety relief valves and pressure relief devices to prevent overpressure situations. The diaphragm is a flexible membrane that is designed to open when the pressure inside the device reaches a certain level, allowing the pressure to be released.
7.What are the considerations for choosing between elastomeric diaphragms and non-elastomeric diaphragms for specific applications?
1. Cost: Elastomeric diaphragms are typically more expensive than non-elastomeric diaphragms.
2. Durability: Elastomeric diaphragms are more durable and can withstand higher pressures and temperatures than non-elastomeric diaphragms.
3. Chemical Compatibility: Elastomeric diaphragms are more resistant to chemical attack than non-elastomeric diaphragms.
4. Flexibility: Elastomeric diaphragms are more flexible than non-elastomeric diaphragms, allowing them to be used in applications where a tight seal is required.
5. Performance: Elastomeric diaphragms are better at maintaining a seal over time than non-elastomeric diaphragms.
8.How are diaphragms designed to resist chemical corrosion and degradation in aggressive environments?
Diaphragms are designed to resist chemical corrosion and degradation in aggressive environments by using materials that are resistant to the specific chemicals present. Common materials used for diaphragms include fluoropolymers, such as PTFE, FEP, and PFA, as well as elastomers, such as EPDM, Viton, and Neoprene. These materials are chosen for their chemical resistance, as well as their ability to withstand extreme temperatures and pressures. Additionally, diaphragms may be coated with a protective layer of a corrosion-resistant material, such as a fluoropolymer or a metal, to further protect them from chemical attack.
9.How do diaphragms provide sealing solutions in hydraulic accumulators and fluid reservoirs?
Diaphragms provide sealing solutions in hydraulic accumulators and fluid reservoirs by creating a barrier between the fluid and the atmosphere. This barrier prevents the fluid from leaking out and keeps the pressure inside the accumulator or reservoir at a constant level. The diaphragm also helps to reduce the amount of air that can enter the system, which helps to reduce the risk of cavitation.
10.Are there specialized diaphragms for high-pressure applications, and what features make them suitable for these conditions?
Yes, there are specialized diaphragms for high-pressure applications. These diaphragms are designed to withstand higher pressures and temperatures than standard diaphragms. They are typically made from reinforced elastomers or metal materials such as stainless steel or Hastelloy. These materials are chosen for their strength and durability, as well as their ability to resist corrosion and wear. Additionally, these diaphragms are designed with thicker walls and reinforced edges to provide additional strength and stability.
11.How do diaphragms maintain their flexibility and resilience over time, and what factors can lead to wear or degradation?
Diaphragms maintain their flexibility and resilience over time by being made of materials that are resistant to wear and tear. Common materials used for diaphragms include rubber, silicone, and polyurethane. These materials are designed to be durable and flexible, and can withstand a wide range of temperatures and pressures.
Factors that can lead to wear or degradation of diaphragms include exposure to extreme temperatures, exposure to chemicals, and physical damage. Additionally, diaphragms can become brittle over time due to age and exposure to the elements. To prevent wear or degradation, it is important to inspect diaphragms regularly and replace them when necessary.
12.Can diaphragms be used in contact with food or pharmaceutical products, and what certifications are required for compliance with industry standards?
Yes, diaphragms can be used in contact with food or pharmaceutical products. Depending on the application, the diaphragm must meet certain industry standards and certifications. For food contact applications, the diaphragm must meet the requirements of the US Food and Drug Administration (FDA) and the European Union (EU) Regulation 10/2011. For pharmaceutical applications, the diaphragm must meet the requirements of the US Pharmacopeia (USP) Class VI and the European Pharmacopoeia (EP).
13.Are there diaphragms made from eco-friendly or sustainable materials for environmentally conscious applications?
Yes, there are diaphragms made from eco-friendly or sustainable materials for environmentally conscious applications. These diaphragms are typically made from natural rubber, silicone, or other biodegradable materials. They are designed to be more durable and longer lasting than traditional diaphragms, and they are also designed to be more energy efficient.
14.Can diaphragms be used in medical devices, and what biocompatibility standards do they need to meet?
Yes, diaphragms can be used in medical devices. The biocompatibility standards that diaphragms need to meet depend on the application and the intended use of the device. Generally, diaphragms used in medical devices must meet the requirements of ISO 10993-1, which outlines the general requirements for biocompatibility. Additionally, depending on the application, the diaphragm may need to meet additional requirements, such as those outlined in ISO 10993-5 for cytotoxicity, ISO 10993-10 for irritation and sensitization, and ISO 10993-11 for hemocompatibility.
15.Are there diaphragms designed for pulsation dampening or shock absorption in hydraulic systems?
Yes, there are diaphragms designed for pulsation dampening and shock absorption in hydraulic systems. These diaphragms are typically made of rubber or elastomeric materials and are designed to absorb the shock and vibration of the hydraulic system. They are often used in applications such as hydraulic cylinders, pumps, and valves.