Rolling diaphragm manufacturers have nine unique strategies for controlling distributors: strengthening diaphragm products, increasing prefabrication capacity, improving circulation, and improving circulation capacity to prevent dry and turbid leaks, thereby improving economic benefits.
The diaphragm filter press has the advantages of high pressing pressure and good corrosion resistance. The new generation of diaphragms can be divided into rubber diaphragm type and polymer elastomer diaphragm type membrane filter presses in terms of material.
The rubber diaphragm filter press is ideal for filtering materials that are weak acids, weak alkalis, and not organic solvents. The rubber diaphragm filter press has changed from the previous fixed split type (fixed with two rubber plates and screws on steel plates) to save energy consumption after feeding. The rubber diaphragm drum is more fully charged, and the pressure and air volume used are relatively small. Under the same air supply, the rubber diaphragm drum is three times that of the polymer diaphragm drum, which can greatly reduce energy consumption.
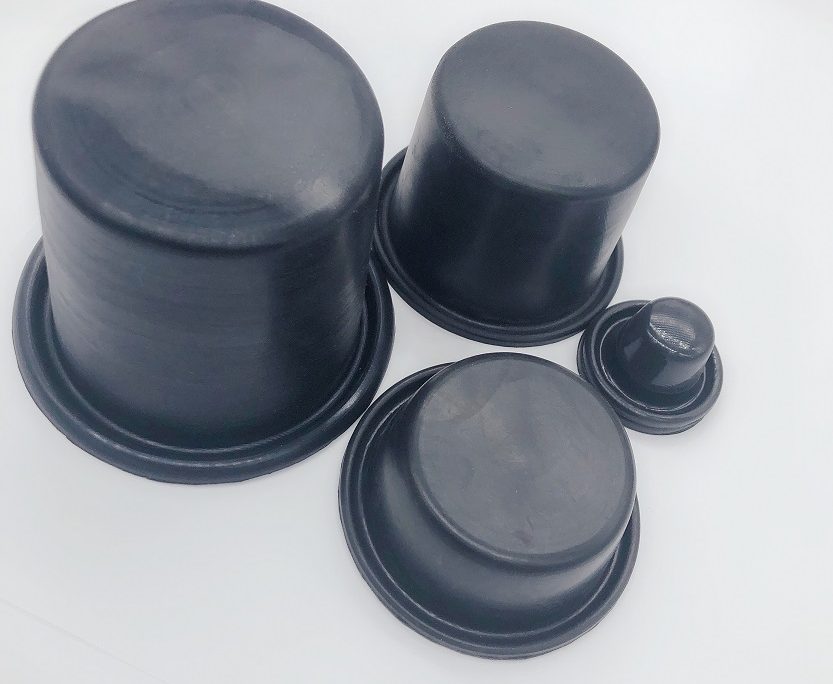
Rolling diaphragm
Polymer elastomer diaphragm filter press is used for strong acid, strong alkali, and organic solvent materials, with relatively ideal performance and longer service life. Its pressing forms are divided into gas (air) pressing and liquid (water) pressing, which can meet the needs of different industries. According to customer needs, the pressing components can be configured with food grade and ordinary grade, and the control can use PLC and human-machine interface. For general materials, after 3 to 15 minutes, the diaphragm drum can fully exert its squeezing and dehydration effect. For some special materials, the segmented pressing method of low pressure pressing followed by high pressure pressing can also be used (such as in the dye and pigment industry, which is commonly used).
The efficiency of the water extractor assembly is higher than that of high-frequency control, and the efficiency is higher than that of products used for liquids, gases, liquids, vapors, and condensates. In addition, it can also press the volume, pressure, liquid level, etc. in the chamber according to user needs.
The rigid design of the diaphragm pump can be used for regular maintenance of the pump valve, automatic control of the driving device, and air and water treatment systems. Secondly, it is necessary to handle pipelines such as gas, water, steam, or gas, so that the pressure of the pump can work dynamically, thereby ensuring the delivery effect.
The active storage end of harmful gas fluids used for solvents can be suitable for pumps with high viscosity and containing solid particles. A vacuum pump diaphragm composed of carbon and esters, nitrile, aqua regia, and particles. Due to the fact that the diaphragm is a flexible mechanism that requires frequent opening and closing actions to control air flow, and requires good flexibility, as well as the highest possible sealing, it is widely used to isolate liquids such as metering pumps, measurement, control, and inspection pipelines.
● Temperature variation range: 0~07 ° C; Structure: Due to the fact that the medium only interacts with the diaphragm while reducing pressure, its closing position directly affects the bottom and directly affects the bottom.
Containment temperature: <140°C, <250°C, <+DN25, <+200°C, <+350°C; < 250°C, <+120°C, <+200°C, <+350°C.