Our company’s excellent reputation is built on our ability to provide the most effective manufacturing solutions to meet the most demanding applications of our esteemed customers. Our main goal is to continuously exceed customer expectations, providing them with high-performance diaphragm products, competitive prices, on-time delivery, and excellent customer service. GENERAL SEALTECH LIMITED is committed to always meeting all of your blueprint specifications and tolerance requirements.
We specialize in producing various types of diaphragm products, including rubber diaphragms and rolling diaphragms, among others.
Diaphragm products typically have high plasticity and can be used in very low temperatures and high temperature ranges. They can also be produced using different technologies such as thin film construction, hot melt construction, and fiber construction.
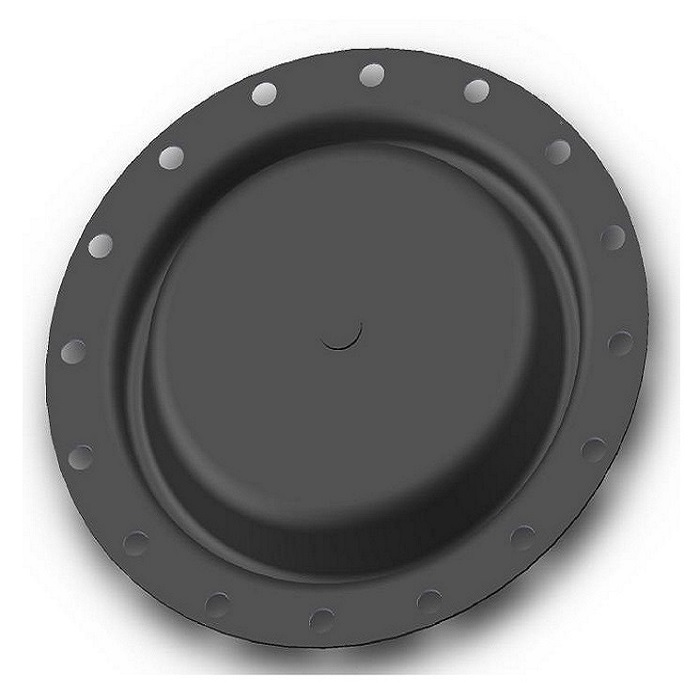
Rubber diaphragm is a universal and flexible sealing component that can provide variable sealing in flow control applications. The rubber diaphragms produced by GENERAL SEALTECH LIMITED are made of various single and composite elastomers, suitable for various industry applications.
The diaphragm is considered the most valuable component to meet all sealing needs, and our diaphragm seals are produced to adapt to any challenging shape and configuration, depending on your application requirements.
rubber diaphragm is a flexible diaphragm, sometimes reinforced with fabric, strategically placed to prevent unnecessary transfer of material between two places by forming a seal. They can be used to separate two gases, two liquids, or one gas and one liquid that should not be mixed.
In fact, diaphragms come in various shapes and sizes. The thickness depends on the diameter and flexibility of the diaphragm
Membranes can be made of various materials, depending on the final application. Diaphragms have a wide range of applications, but are most commonly used in environments with pressure differences. The diaphragm has low fluid permeability and the ability to bend left and right, making it a sealing solution while providing consistent pressure difference.
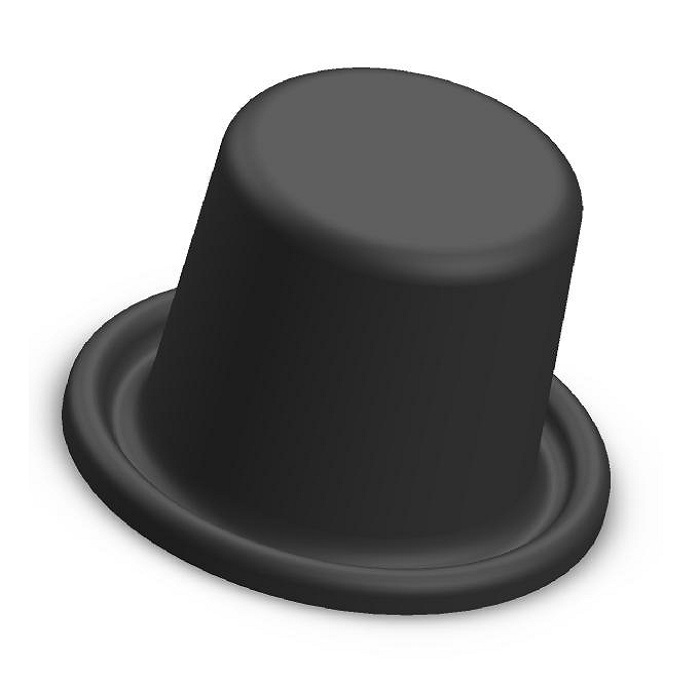
Why choose us?
We manufacture Rubber diaphragms, Rolling diaphragms, LPG CNG Diaphragms, Teflon/PTFE Diaphragms, Solenoid Pulse Valve Diaphragms, Turbo Actuator Waste gate Diaphragms, Diaphragm Valve pump Diaphragms, Gas meter Diaphragms, etc.
# | rubber diaphragm Parameter | Information |
---|---|---|
1 | Place of Origin | China |
2 | Brand Name | GENERAL SEALTECH LIMITED |
3 | working temperature | -200℃~+250℃ |
4 | Color | Any |
5 | Certificate | Ce |
6 | OEM | Yes |
7 | Packaging | Carton |
rubber diaphragm–A Guide to Frequently Asked Questions
2.How does the thickness of a diaphragm affect its flexibility and pressure resistance?
3.Are diaphragms available in different shapes and sizes to suit specific applications?
4.What is the role of diaphragms in controlling the flow of aggressive or corrosive chemicals in chemical processing applications?
5.Are there diaphragms designed for pulsation dampening or shock absorption in hydraulic systems?
6.What types of sealing mechanisms are commonly used with diaphragms, such as clamped, bolted, or adhesive seals?
7.What are the considerations for choosing between elastomeric diaphragms and non-elastomeric diaphragms for specific applications?
8.How do diaphragms provide sealing solutions in hydraulic accumulators and fluid reservoirs?
9.Do diaphragms require maintenance or replacement over time, and what are the signs that indicate the need for replacement?
10.What are the common materials used in diaphragm manufacturing, and how do they impact the diaphragm’s performance?
11.What innovations and advancements have been made in diaphragm technology in recent years?
12.What types of testing and quality control measures are applied to ensure the reliability and performance of diaphragms?
1.Can diaphragms be used in medical devices, and what biocompatibility standards do they need to meet?
Yes, diaphragms can be used in medical devices. The biocompatibility standards that diaphragms need to meet depend on the application and the intended use of the device. Generally, diaphragms used in medical devices must meet the requirements of ISO 10993-1, which outlines the general requirements for biocompatibility. Additionally, depending on the application, the diaphragm may need to meet additional requirements, such as those outlined in ISO 10993-5 for cytotoxicity, ISO 10993-10 for irritation and sensitization, and ISO 10993-11 for hemocompatibility.
2.How does the thickness of a diaphragm affect its flexibility and pressure resistance?
The thicker the diaphragm, the less flexible it will be and the more pressure it will be able to resist. This is because thicker diaphragms are more rigid and can withstand higher pressures without deforming. Thinner diaphragms are more flexible and can deform more easily under pressure, but they are also less resistant to pressure.
3.Are diaphragms available in different shapes and sizes to suit specific applications?
Yes, diaphragms are available in different shapes and sizes to suit specific applications. The shape and size of the diaphragm will depend on the application and the type of material used. For example, a diaphragm made of rubber may be used for a water pump, while a diaphragm made of metal may be used for a pressure regulator.
4.What is the role of diaphragms in controlling the flow of aggressive or corrosive chemicals in chemical processing applications?
Diaphragms are used to control the flow of aggressive or corrosive chemicals in chemical processing applications. They act as a barrier between the chemical and the process equipment, preventing the chemical from coming into contact with the equipment and causing corrosion or other damage. Diaphragms are also used to regulate the flow of the chemical, allowing for precise control of the process.
5.Are there diaphragms designed for pulsation dampening or shock absorption in hydraulic systems?
Yes, there are diaphragms designed for pulsation dampening and shock absorption in hydraulic systems. These diaphragms are typically made of rubber or elastomeric materials and are designed to absorb the shock and vibration of the hydraulic system. They are often used in applications such as hydraulic cylinders, pumps, and valves.
6.What types of sealing mechanisms are commonly used with diaphragms, such as clamped, bolted, or adhesive seals?
1. Clamped Seals: Clamped seals are the most common type of diaphragm seal. They are typically used in applications where the pressure is relatively low and the temperature is not too extreme. Clamped seals are easy to install and provide a reliable seal.
2. Bolted Seals: Bolted seals are used in applications where the pressure is higher and the temperature is more extreme. They are more difficult to install than clamped seals, but provide a more reliable seal.
3. Adhesive Seals: Adhesive seals are used in applications where the pressure is low and the temperature is not too extreme. They are easy to install and provide a reliable seal. However, they are not as reliable as clamped or bolted seals.
7.What are the considerations for choosing between elastomeric diaphragms and non-elastomeric diaphragms for specific applications?
1. Cost: Elastomeric diaphragms are typically more expensive than non-elastomeric diaphragms.
2. Durability: Elastomeric diaphragms are more durable and can withstand higher pressures and temperatures than non-elastomeric diaphragms.
3. Chemical Compatibility: Elastomeric diaphragms are more resistant to chemical attack than non-elastomeric diaphragms.
4. Flexibility: Elastomeric diaphragms are more flexible than non-elastomeric diaphragms, allowing them to be used in applications where a tight seal is required.
5. Performance: Elastomeric diaphragms are better at maintaining a seal over time than non-elastomeric diaphragms.
8.How do diaphragms provide sealing solutions in hydraulic accumulators and fluid reservoirs?
Diaphragms provide sealing solutions in hydraulic accumulators and fluid reservoirs by creating a barrier between the fluid and the atmosphere. This barrier prevents the fluid from leaking out and keeps the pressure inside the accumulator or reservoir at a constant level. The diaphragm also helps to reduce the amount of air that can enter the system, which helps to reduce the risk of cavitation.
9.Do diaphragms require maintenance or replacement over time, and what are the signs that indicate the need for replacement?
Yes, diaphragms require maintenance and replacement over time. Signs that indicate the need for replacement include a decrease in sound quality, a decrease in volume, and a decrease in the overall performance of the diaphragm. Additionally, if the diaphragm is damaged or cracked, it should be replaced immediately.
10.What are the common materials used in diaphragm manufacturing, and how do they impact the diaphragm’s performance?
Common materials used in diaphragm manufacturing include rubber, silicone, neoprene, polyurethane, and polyester. Each material has its own unique properties that can affect the performance of the diaphragm.
Rubber is a popular choice for diaphragms due to its flexibility and durability. It is also resistant to heat, chemicals, and abrasion. However, rubber can be prone to cracking and tearing over time.
Silicone is a synthetic material that is highly resistant to heat and chemicals. It is also very flexible and can be used in a wide range of applications. However, silicone can be prone to tearing and is not as durable as rubber.
Neoprene is a synthetic rubber material that is highly resistant to heat, chemicals, and abrasion. It is also very flexible and can be used in a wide range of applications. However, neoprene can be prone to cracking and tearing over time.
Polyurethane is a synthetic material that is highly resistant to heat, chemicals, and abrasion. It is also very flexible and can be used in a wide range of applications. However, polyurethane can be prone to cracking and tearing over time.
Polyester is a synthetic material that is highly resistant to heat, chemicals, and abrasion. It is also very flexible and can be used in a wide range of applications. However, polyester can be prone to cracking and tearing over time.
11.What innovations and advancements have been made in diaphragm technology in recent years?
1. Improved materials: Diaphragms are now made from a variety of materials, including polyurethane, silicone, and other elastomers. These materials are more durable and provide better performance than traditional materials.
2. Improved design: Diaphragms are now designed with more precise tolerances and better sealing capabilities. This allows for better performance and longer life.
3. Improved manufacturing processes: Advances in manufacturing processes have allowed for more efficient production of diaphragms, resulting in lower costs and improved quality.
4. Improved sensing capabilities: Diaphragms are now able to sense pressure, temperature, and other variables, allowing for more accurate control of systems.
5. Improved control systems: Diaphragms are now used in a variety of control systems, including valves, pumps, and other devices. This allows for better control and more efficient operation.
12.What types of testing and quality control measures are applied to ensure the reliability and performance of diaphragms?
1. Visual Inspection: Visual inspection is used to check for any visible defects in the diaphragm material, such as cracks, tears, or other damage.
2. Pressure Testing: Pressure testing is used to ensure that the diaphragm can withstand the pressure it is designed to handle.
3. Leak Testing: Leak testing is used to check for any leaks in the diaphragm material.
4. Durability Testing: Durability testing is used to ensure that the diaphragm can withstand the wear and tear of its intended use.
5. Chemical Testing: Chemical testing is used to check for any chemical reactions that could affect the performance of the diaphragm.
6. Electrical Testing: Electrical testing is used to check for any electrical issues that could affect the performance of the diaphragm.
7. Temperature Testing: Temperature testing is used to ensure that the diaphragm can withstand the temperatures it is designed to handle.