Our company’s excellent reputation is built on our ability to provide the most effective manufacturing solutions to meet the most demanding applications of our esteemed customers. Our main goal is to continuously exceed customer expectations, providing them with high-performance diaphragm products, competitive prices, on-time delivery, and excellent customer service. GENERAL SEALTECH LIMITED is committed to always meeting all of your blueprint specifications and tolerance requirements.
We specialize in producing various types of diaphragm products, including rubber diaphragms and rolling diaphragms, among others.
The design principle of a fuel pump diaphragm rubber is to use the failure strength and failure mode of materials or structures to set personalized control strategies for a certain heat or mass transfer medium, or for the occurrence of certain flow or diffusion effects, in order to achieve specific functions or protocols.
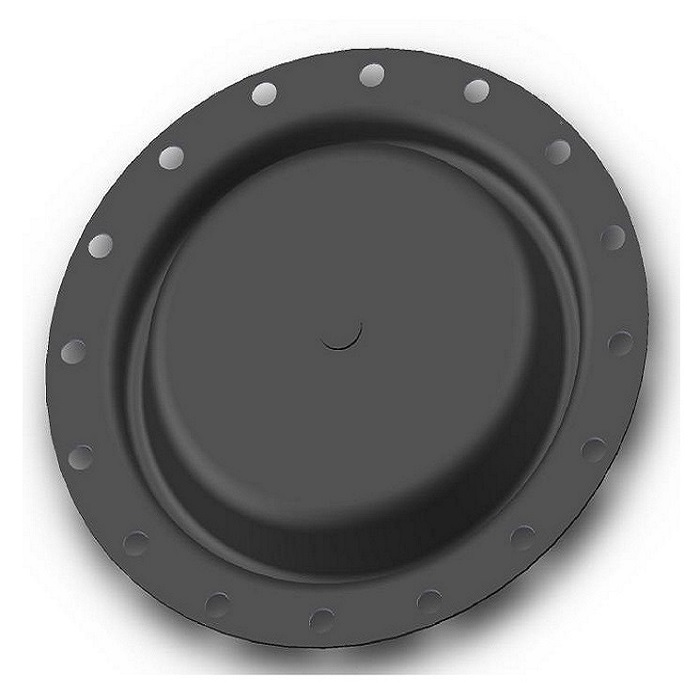
Fuel pump diaphragm rubber is a universal and flexible sealing component that can provide variable sealing in flow control applications. The rubber diaphragms produced by GENERAL SEALTECH LIMITED are made of various single and composite elastomers, suitable for various industry applications.
The diaphragm is considered the most valuable component to meet all sealing needs, and our diaphragm seals are produced to adapt to any challenging shape and configuration, depending on your application requirements.
Fuel pump diaphragm rubber is a flexible diaphragm, sometimes reinforced with fabric, strategically placed to prevent unnecessary transfer of material between two places by forming a seal. They can be used to separate two gases, two liquids, or one gas and one liquid that should not be mixed.
In fact, diaphragms come in various shapes and sizes. The thickness depends on the diameter and flexibility of the diaphragm
Membranes can be made of various materials, depending on the final application. Diaphragms have a wide range of applications, but are most commonly used in environments with pressure differences. The diaphragm has low fluid permeability and the ability to bend left and right, making it a sealing solution while providing consistent pressure difference.
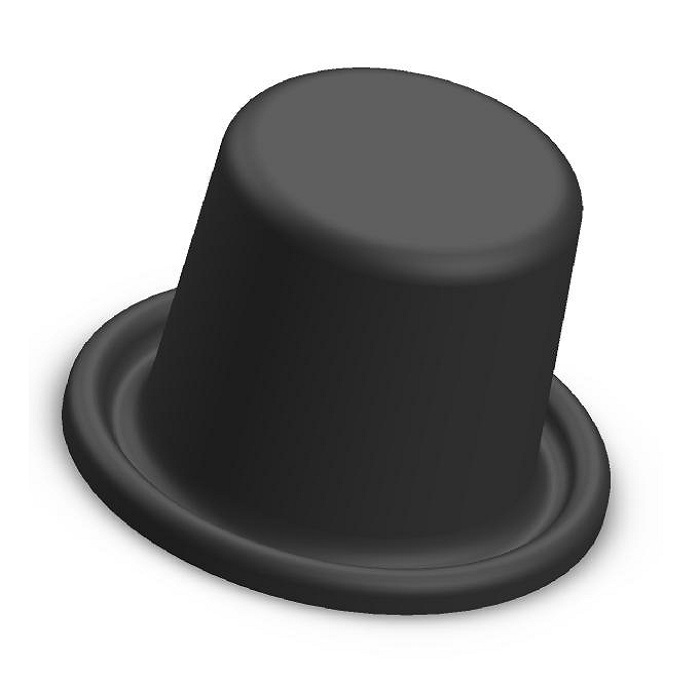
Why choose us?
- 1We manufacture Rubber diaphragms, Rolling diaphragms, LPG CNG Diaphragms, Teflon/PTFE Diaphragms, Solenoid Pulse Valve Diaphragms, Turbo Actuator Waste gate Diaphragms, Diaphragm Valve pump Diaphragms, Gas meter Diaphragms, etc.
Fuel pump diaphragm rubber–A Guide to Frequently Asked Questions
2.How do diaphragms perform in high-vibration environments, and what measures are taken to ensure their reliability in these conditions?
3.Can diaphragms be customized for specific applications?
4.Are there diaphragms designed for pulsation dampening or shock absorption in hydraulic systems?
5.What role do fuel pump diaphragm rubber play in controlling fluid flow and preventing leaks in pumps and valves?
6.Are there diaphragms designed for use in critical industries such as aerospace and healthcare, and what unique properties do they possess?
7.Are fuel pump diaphragm rubber available in different shapes and sizes to suit specific applications?
8.What mechanical and industrial applications can diaphragms be used in?
9.How does the thickness of a diaphragm affect its flexibility and pressure resistance?
1.How do fuel pump diaphragm rubber contribute to the isolation of different process media or gases within a system?
fuel pump diaphragm rubber are used to separate different process media or gases within a system by creating a physical barrier between them. This barrier prevents the media or gases from mixing, thus providing a degree of isolation. Diaphragms are also used to control the flow of media or gases within a system, as they can be designed to open and close in response to pressure or other external factors.
2.How do diaphragms perform in high-vibration environments, and what measures are taken to ensure their reliability in these conditions?
Diaphragms are designed to be highly reliable in high-vibration environments. To ensure their reliability, measures such as using thicker diaphragm material, using multiple layers of material, and using dampening materials such as rubber or foam are taken. Additionally, the diaphragm should be securely mounted to the structure to prevent it from vibrating excessively. Finally, the diaphragm should be inspected regularly to ensure that it is not damaged or worn out.
3.Can diaphragms be customized for specific applications?
Yes, diaphragms can be customized for specific applications. Depending on the application, the diaphragm can be made from different materials, such as rubber, plastic, or metal, and can be designed to meet specific requirements.
4.Are there diaphragms designed for pulsation dampening or shock absorption in hydraulic systems?
Yes, there are diaphragms designed for pulsation dampening and shock absorption in hydraulic systems. These diaphragms are typically made of rubber or elastomeric materials and are designed to absorb the shock and vibration of the hydraulic system. They are often used in applications such as hydraulic cylinders, pumps, and valves.
5.What role do fuel pump diaphragm rubber play in controlling fluid flow and preventing leaks in pumps and valves?
fuel pump diaphragm rubber are flexible membranes that are used to control fluid flow and prevent leaks in pumps and valves. They are typically made of rubber or plastic and are designed to flex and move in response to pressure changes. When pressure is applied to one side of the diaphragm, it flexes and creates a seal that prevents fluid from leaking out. This seal is maintained until the pressure is released, allowing the diaphragm to return to its original shape and allowing the fluid to flow freely. Diaphragms are used in a variety of applications, including pumps, valves, and other fluid control systems.
6.Are there diaphragms designed for use in critical industries such as aerospace and healthcare, and what unique properties do they possess?
Yes, there are diaphragms designed for use in critical industries such as aerospace and healthcare. These diaphragms are typically made from high-performance materials such as PTFE, FKM, and EPDM, which offer superior chemical and temperature resistance, as well as excellent durability and strength. Additionally, these diaphragms are designed to meet the stringent requirements of these industries, such as tight tolerances, high-pressure ratings, and low-leakage rates.
7.Are fuel pump diaphragm rubber available in different shapes and sizes to suit specific applications?
Yes, fuel pump diaphragm rubber are available in different shapes and sizes to suit specific applications. The shape and size of the diaphragm will depend on the application and the type of material used. For example, a diaphragm made of rubber may be used for a water pump, while a diaphragm made of metal may be used for a pressure regulator.
8.What mechanical and industrial applications can diaphragms be used in?
1. Pumps: Diaphragms are used in pumps to separate the pump chamber from the motor, allowing the pump to move fluid without the motor becoming contaminated.
2. Valves: Diaphragms are used in valves to control the flow of liquids and gases.
3. Compressors: Diaphragms are used in compressors to create a seal between the compressor and the cylinder, allowing the compressor to compress the air or gas.
4. Actuators: Diaphragms are used in actuators to convert energy into motion.
5. Filters: Diaphragms are used in filters to separate particles from liquids and gases.
6. Seals: Diaphragms are used in seals to create a tight seal between two surfaces.
7. Pressure Vessels: Diaphragms are used in pressure vessels to contain and control the pressure of a gas or liquid.
8. Heat Exchangers: Diaphragms are used in heat exchangers to separate two fluids while allowing heat to transfer between them.
9.How does the thickness of a diaphragm affect its flexibility and pressure resistance?
The thicker the diaphragm, the less flexible it will be and the more pressure it will be able to resist. This is because thicker diaphragms are more rigid and can withstand higher pressures without deforming. Thinner diaphragms are more flexible and can deform more easily under pressure, but they are also less resistant to pressure.
Tags: Turbo Actuator Waste-gate Diaphragms , Solenoid Pulse Valve Diaphragms