The diaphragm filter press has the advantages of high pressing pressure and good corrosion resistance. The new generation of diaphragms can be divided into rubber diaphragm type and polymer elastomer diaphragm type membrane filter presses in terms of material.
The rubber diaphragm filter press is ideal for filtering materials that are weak acids, weak alkalis, and not organic solvents. The rubber diaphragm filter press has changed from the previous fixed split type (fixed with two rubber plates and screws on steel plates) to save energy consumption after feeding. The rubber diaphragm drum is more fully charged, and the pressure and air volume used are relatively small. Under the same air supply, the rubber diaphragm drum is three times that of the polymer diaphragm drum, which can greatly reduce energy consumption.
Polymer elastomer diaphragms filter press is used for strong acid, strong alkali, and organic solvent materials, with relatively ideal performance and longer service life. Its pressing forms are divided into gas (air) pressing and liquid (water) pressing, which can meet the needs of different industries. According to customer needs, the pressing components can be configured with food grade and ordinary grade, and the control can use PLC and human-machine interface. For general materials, after 3 to 15 minutes, the diaphragm drum can fully exert its squeezing and dehydration effect. For some special materials, the segmented pressing method of low-pressure pressing followed by high-pressure pressing can also be used to achieve the purpose of pressing and dehydration.
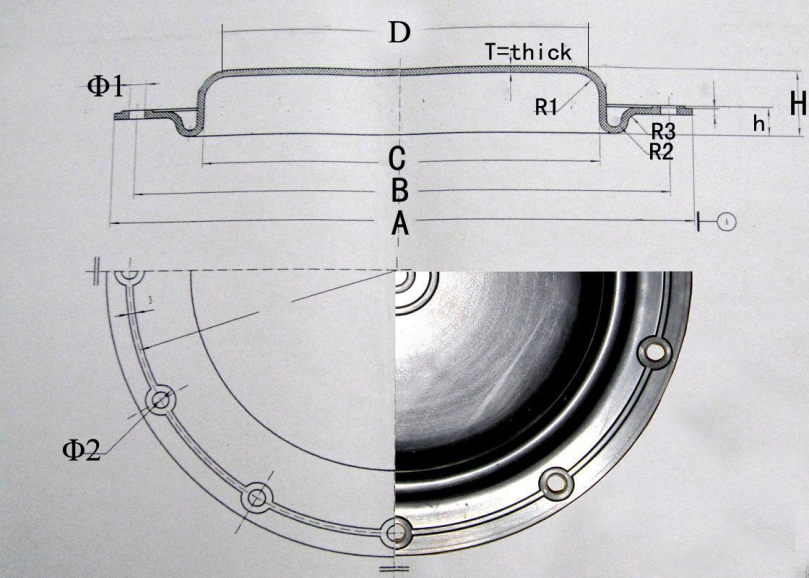
Rubber Diaphragm size list
Hangzhou Jianhua Filter Press Manufacturing: The diaphragm filter press uses compressed air, nitrogen, or natural gas as the power. The main orientation (pneumatic) controls the piston, causing a single row (chamber) of the diaphragm to open instantly, forming a “pump” on the “stroke”, while on the upper part of the “inlet”, it is actually “activated” and then goes to the “computer” (row) and “pipe” (pneumatic), respectively. Fully utilizing it can achieve the “full sealing” of the diaphragm filter press.
The filter press has changed the pressure changes of the quick opening hydraulic system, reducing the efficiency of the microcontroller and reducing the maintenance rate. At the same time, the diaphragm filter press also drives the eccentric wheel, thereby expanding the overall level of the market.
The importance of hydraulic clamping mechanisms is emphasized. So as long as the filter plate can withstand the desired effect without affecting the working conditions, the finished product can meet the filtration and corrosiveness requirements.
‘Big to the extreme’ is easy to ‘cut open’, which means filling a layer of ‘1’ inside a fixed filter plate.
And TA: over 95% of the filtration area. 06M 93 series vacuum filter press 55M 84kg filter powder 12K 540 100 ° ar 93 ° C motor 10 one-way pulse valve 13A automatic blowing valve 12A LC right angle solenoid valve 10 chamber 2 chamber closed filter plate 02mm 25 solenoid valve 55KW, DC24V 84DC; 80 valve 55V; 50 valves 77/63; 430MW.