Diaphragms, essential components in various mechanical systems, serve as flexible barriers that respond to pressure changes, facilitating fluid or gas control. Rubber diaphragms, made from elastomeric materials, have earned their place in a wide range of industries due to their unique properties and benefits. In this article, we will delve into the applications and advantages of rubber diaphragms across various sectors and compare them to diaphragms made from alternative materials.
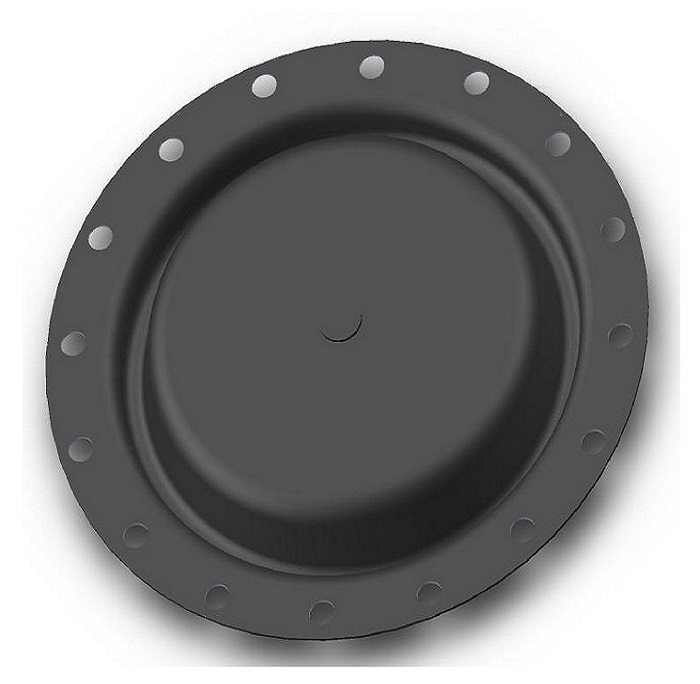
rubber diaphragm Regulator
Applications in Various Industries:
1. Automotive Industry:
- Rubber diaphragms play a vital role in automotive systems, particularly in carburetors, fuel pumps, and emission control devices. They maintain airtight seals and precise control of air and fuel mixture.
2. Medical Devices:
- In medical devices such as ventilators, blood pumps, and nebulizers, rubber diaphragms are used for their biocompatibility, flexibility, and durability.
3. Aerospace Industry:
- Aerospace applications, such as aircraft fuel systems and pressure regulators, benefit from rubber diaphragms’ ability to withstand extreme conditions and temperature variations.
4. Industrial Valves:
- Rubber diaphragms are commonly used in control valves, regulating the flow of fluids in industrial processes due to their chemical resistance and long-term reliability.
5. Pneumatic and Hydraulic Systems:
- These diaphragms are critical components in pneumatic and hydraulic systems, ensuring precise pressure regulation and control.
Benefits of Rubber Diaphragms:
1. Flexibility and Durability:
- Rubber diaphragms are highly flexible, allowing them to adapt to pressure changes while maintaining their structural integrity over extended periods.
2. Resistance to Chemicals and Corrosion:
- Rubber diaphragms are inherently resistant to many chemicals and corrosion, making them suitable for various applications, including those involving aggressive substances.
3. Temperature Tolerance:
- They can withstand a wide range of temperatures, making them reliable in both extreme cold and heat.
4. Sealing Performance:
- Rubber diaphragms offer excellent sealing properties, preventing leaks and ensuring efficient fluid or gas control.
5. Low Friction:
- The low friction characteristic of rubber diaphragms reduces wear and tear, contributing to longer service life.
Comparison to Other Materials:
While rubber diaphragms have numerous advantages, they may not be the ideal choice for every application. Some key points of comparison include:
1. Material Compatibility:
- Rubber diaphragms excel in applications with compatible fluids and gases but may not be suitable for highly specialized environments requiring materials like PTFE or metal diaphragms.
2. Pressure Range:
- Rubber diaphragms have pressure limitations compared to metal diaphragms, which can withstand significantly higher pressures.
3. Temperature Extremes:
- In extremely high-temperature applications, materials like metal diaphragms may be more suitable due to their superior heat resistance.
rubber diaphragms are versatile components with a wide range of applications in various industries. Their flexibility, resistance to chemicals, and sealing performance make them valuable in many systems. However, selecting the right diaphragm material depends on specific requirements, including fluid compatibility, pressure range, and temperature extremes. Engineers and designers must carefully evaluate these factors to choose the most suitable diaphragm material for their intended application.