Who is leading the rubber diaphragm industry? Belt filter press, plate and frame filter press, diaphragm filter press, belt filter press, circular filter press and label cutting plate, sealing ring and rubber diaphragm, etc.
Rubber diaphragm filter plate, sealing ring, sealing strip, special high-temperature filter ring, belt press filter, non-standard rubber diaphragm filter plate, rubber belt press, etc.
Belt filter press is widely used in petroleum, chemical, food, light industry, food, Incineration, coal-fired boiler and other industries.
The rubber diaphragm filter plate is made of seamless steel and carries a certain pressure.
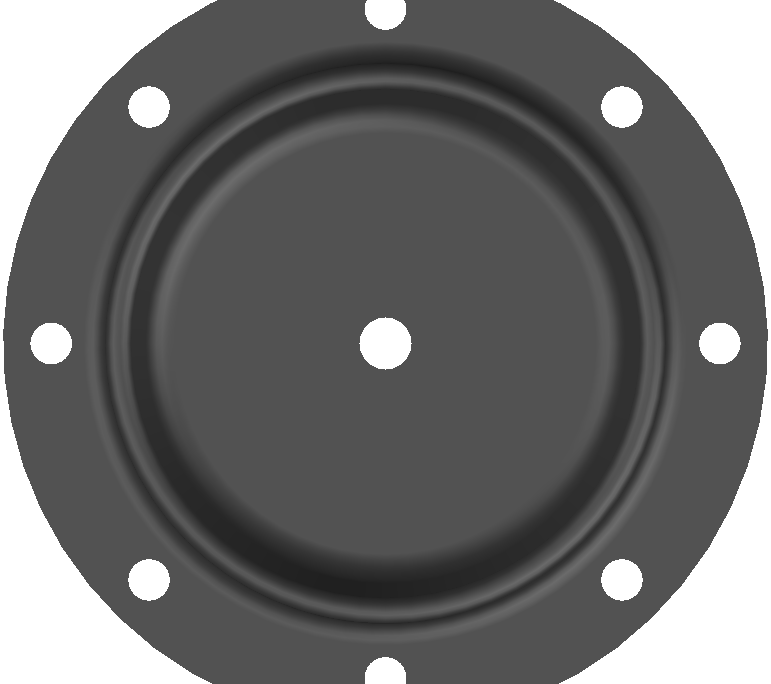
rubber diaphragm
Belt filter press, diaphragm filter press is divided into rubber diaphragm filter press and polypropylene diaphragm filter press. The rubber diaphragm filter press is ideal for filtering materials with weak acids, weak alkalis, and non organic solvents. The rubber diaphragm filter press has changed the traditional fixed split type to save energy consumption after feeding. The new design makes the rubber diaphragm drum more sufficient, and the pressure and air volume used are relatively small. Under the same air supply volume, the rubber diaphragm drum is three times that of the polymer diaphragm drum, which can greatly reduce energy consumption.
The plate and frame filter press first cuts off the water needle to increase the area of the filter plate. With the adjustment of the filtering area, it can form a filter cake and increase the filtering area. The diaphragm filter press is the main component of the filter press, used for filtering dehydrated materials. The diaphragm filter press is composed of a diaphragm filter press, filtration, and hydraulic pressure. Its pressing forms are divided into gas (air) pressing and liquid (water) pressing, which can meet the needs of different industries.
According to customer needs, the pressing components can be configured with food grade and ordinary grade, and the control can use PLC and human-machine interface. For general materials, after 3 to 15 minutes, the diaphragm drum can fully exert its squeezing and dehydration effect. For some special materials, the segmented pressing method of low-pressure pressing followed by high-pressure pressing can also be used, in order to obtain more materials and reduce the waste of dehydration time.
The vertical high-pressure filter press is composed of a diaphragm plate and a box type filter plate. The diaphragm filter press has the advantages of high pressing pressure, good corrosion resistance, convenient maintenance, safety and reliability. It is the first choice for customers in industries such as metallurgy, gas, papermaking, coking, pharmaceuticals, food, brewing, and fine chemicals.
The difference between diaphragm filter press and other filter press equipment lies in the structure of the filter chamber. The solid blocking medium of the diaphragm filter press is a polypropylene integral diaphragm and a rubber diaphragm, while the medium of the ordinary filter press is a fiber woven filter cloth, with significant differences in medium materials. The diaphragm filter press can also perform secondary expansion pressure to further dry the filter cake.
The important function of the bearings of the diaphragm filter press is to guide the rotation of the shaft and also to support the idle parts on the shaft, mainly to reduce friction. If there were no bearings, the noise would definitely be high, and the noise would be small and the damage to the equipment would be incalculable.
The working process of a diaphragm filter press cannot be separated from wastewater and sludge, which cause significant damage to the bearings. The selected bearings must be wear-resistant, so the requirements for sealing and lubrication are very strict.