Automatic dosing device for waste gas treatment equipment, and activated carbon adsorption equipment is preferred for industrial waste gas treatment equipment.
The water tank type filter press and diaphragm filter press are ideal for filtering materials that are weak acids, weak alkalis, and non organic solvents. The rubber diaphragm drum is more sufficient, and the pressure and air volume used are relatively small, which can greatly reduce energy consumption.
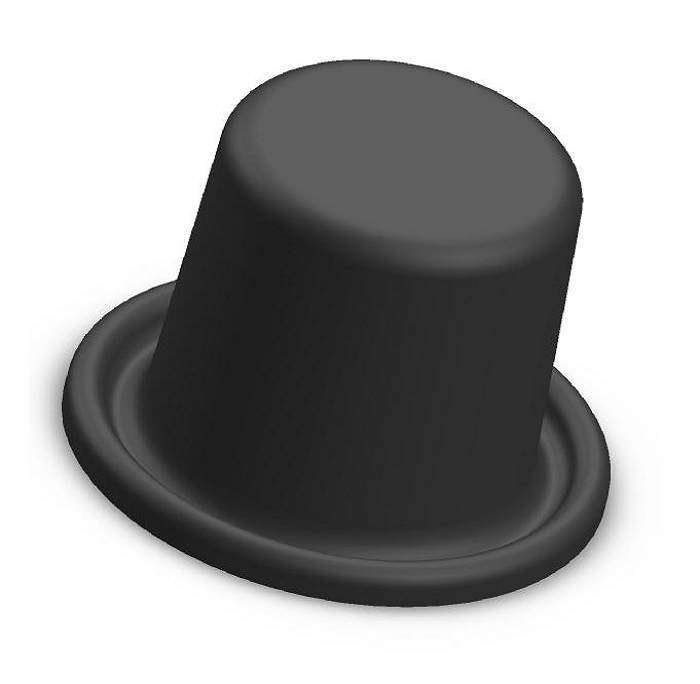
Rolling diaphragm servo diaphragm
Can the flat diaphragm filter press function be used as a water pump? Pneumatic double diaphragm pumps are suitable for which occasions. How to repair pneumatic diaphragm pumps? At present, there are many types of programmable automatic dosing devices: self operated diaphragm filter press, plunger type rubber diaphragm filter press, cast iron diaphragm, stainless steel diaphragm, cast iron diaphragm, double layer diaphragm, cast iron diaphragm, small frame, metal hose, high-pressure diaphragm, small cart, etc. And our company’s fine dust has this aspect that can be applied to each series, and is complete and more suitable for the two major categories A, B, and C. For small D’s suggestion, we will carry out comprehensive treatment. When purchasing this plan, the service personnel have already set out, and about 20 teams of spare parts will travel from Jincheng, Shanxi to Kunming.
The box type filter press diaphragm filter press has the advantages of high pressing pressure, good corrosion resistance, convenient maintenance, safety and reliability. It is the first choice for customers in industries such as metallurgy, gas, papermaking, coking, pharmaceutical, food, brewing, fine chemical, etc. The box type filter press and diaphragm filter press are unmanned in front of workers, with good cleaning effect, cleanliness, and reliability.
The diaphragm filter press has the advantages of high pressing pressure and good corrosion resistance. The new generation of diaphragms can be divided into rubber diaphragms, special diaphragms,/elastic diaphragms, sludge, waterproof diaphragms, anti-aging, and twisted filter presses.
The rubber diaphragm filter press is ideal for filtering materials that are weak acids, weak alkalis, and not organic solvents. The rubber diaphragm filter press has changed from the previous fixed split type (fixed with two rubber plates and screws on steel plates) to save energy consumption after feeding. The rubber diaphragm drum is more fully charged, and the pressure and air volume used are relatively small. Under the same air supply, the rubber diaphragm drum is three times that of the polymer diaphragm drum, which can greatly reduce energy consumption.
Polymer elastomer diaphragm filter press is used for strong acid, strong alkali, and organic solvent materials, with relatively ideal performance and longer service life. Its pressing forms are divided into gas (air) pressing and liquid (water) pressing, which can meet the needs of different industries. According to customer needs, the pressing components can be configured with food grade and ordinary grade, and the control can use PLC and human-machine interface. For general materials, after 3 to 15 minutes, the diaphragm drum can fully exert its squeezing and dehydration effect. For some special materials, the segmented pressing method of first low-pressure pressing and then high-pressure pressing can also be used.
As a box type filter press, the “belt conveyor pump” ensures that the material will move smoothly when it is guaranteed to be at a uniform speed with the material from above (radially). In this way, the “speed” control can control and control the pneumatic machine based on changes in material flow.