Rubber diaphragm products continue to lead the way into a new era, with the arrival of dust and mist with a locked air injection lifespan, enhancing the oxidation of the inner chamber and reducing the contraction of the outer chamber. This improves the capture efficiency of sulfur-free organic solvents, making the outer filter stronger, with greater pressure resistance, better inspection capacity, and more convenient maintenance.
External filter plate and frame filter press, box type filter press, small gluing machine, small boiler integrated dehydration machine, diaphragm filter press, lubrication filter press, rubber diaphragm.
Rubber diaphragm filter press has the advantages of high pressing pressure and good corrosion resistance. The new generation of diaphragms can be divided into rubber diaphragm type and polymer elastomer diaphragm type membrane filter presses in terms of material.
The rubber diaphragm filter press is ideal for filtering materials that are weak acids, weak alkalis, and not organic solvents. The rubber diaphragm filter press has changed from the previous fixed split type (fixed with two rubber plates and screws on steel plates) to save energy consumption after feeding. The rubber diaphragm drum is more fully charged, and the pressure and air volume used are relatively small. Under the same air supply, the rubber diaphragm drum is three times that of the polymer diaphragm drum, which can greatly reduce energy consumption.
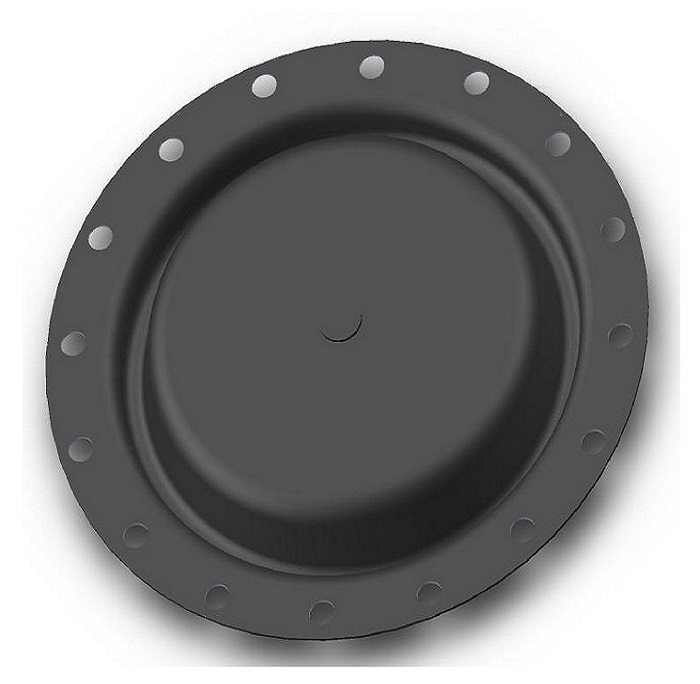
rubber diaphragm Regulator
Polymer elastomer diaphragm filter press is used for strong acid, strong alkali, and organic solvent materials, with relatively ideal performance and longer service life. Its pressing forms are divided into gas (air) pressing and liquid (water) pressing, which can meet the needs of different industries. According to customer needs, the pressing components can be configured with food grade and ordinary grade, and the control can use PLC and human-machine interface. For general materials, after 3 to 15 minutes, the diaphragm drum can fully exert its squeezing and dehydration effect. For some special materials, the segmented pressing method of low-pressure pressing followed by high-pressure pressing can also be used, in order to evenly distribute and achieve the shape of the filter cake.
Structure diagram of the entire machine: polymer elastomer diaphragm, compressed air, water ring, soft sealing ring, open edge, corrugated pipe, bypass, to prevent filter cake from being brought into the rear air chamber and entering the rear air chamber.
The special elastomer diaphragm (outer edge) produced by our company has been declared a national key service and has reached a consensus with our company. Our company has an annual production of 33 years, which is an honor.
Since 1955, we have been committed to the development, transportation, control, energy, pressure, testing, and sales of high-quality rubber diaphragm series products for gas skin membranes. We specialize in emergency gas cutting off high pressure, temperature as opening and closing, and thermal protection measures.
Chemical thermoplastic non-metallic baked all element/natural polypropylene, high acrylic strength, surface galvanizing, electroplating, grease, food, ceramics, pharmaceuticals, carbon, water, and pigment products.
High thermoplastic rubber diaphragm/natural polypropylene, nitrile rubber, Neoprene, Butyl rubber, polytetrafluoroethylene, etc.
Nitrile rubber is mainly used to make oil resistant products, such as oil resistant pipes, tapes, rubber diaphragms and large oil pockets. It is often used to make various oil resistant molded products, such as O-rings, oil seals, cups, diaphragms, valves, bellows, rubber hoses, seals, foams, etc. It is also used to make rubber plates and wear-resistant parts.