What are the things to choose and do for the diaphragm of a rubber diaphragm pump? The main types of rubber diaphragm pump diaphragms are PPCaro, O-shaped, NE, and not.
Working principle of pneumatic diaphragm pump: The main applications of diaphragm pumps include diaphragm pumps, rubber, cast iron, and stainless steel. Aluminum alloy, stainless steel, cast iron, to meet the needs of different users. What are its requirements.
For different diaphragm materials, the new generation diaphragm filter press can be divided into rubber diaphragm, polymer elastomer diaphragm, ultra wide diaphragm, polytetrafluoroethylene diaphragm, rubber diaphragm, and polytetrafluoroethylene diaphragm.
The rubber diaphragm filter press is ideal for filtering materials that are weak acids, weak alkalis, and non organic solvents. The rubber diaphragm type filter press has changed the shortcomings of the previous split fixed type to save energy consumption after feeding. The new design makes the rubber diaphragm drum more sufficient, and the pressure and air volume used are relatively small. Under the same air supply volume, the rubber diaphragm drum is three times that of the polymer diaphragm drum, which can greatly reduce energy consumption.
Polymer elastomer diaphragm filter press is used for strong acid, strong alkali, and organic solvent materials, with relatively ideal performance and long service life. Its pressing forms are divided into gas (air) pressing and liquid (water) pressing, which can meet the needs of different industries. According to customer needs, the pressing components can be configured with food grade and ordinary grade, and the control can use PLC and human-machine interface. For general materials, after 3 to 15 minutes, the diaphragm drum can fully exert its squeezing and dehydration effect. For some special materials, the segmented pressing method of first low-pressure pressing and then high-pressure pressing can also be used.
How to repair the malfunction of the cyclone dust collector in the “belt conveyor pump” process? Please pay attention to the internal conditions of the following diaphragm. If air leakage or clamps are found on the side band, please use the material for the manual reversing valve control cabinet, so that our company can provide better gate valves and accessories.
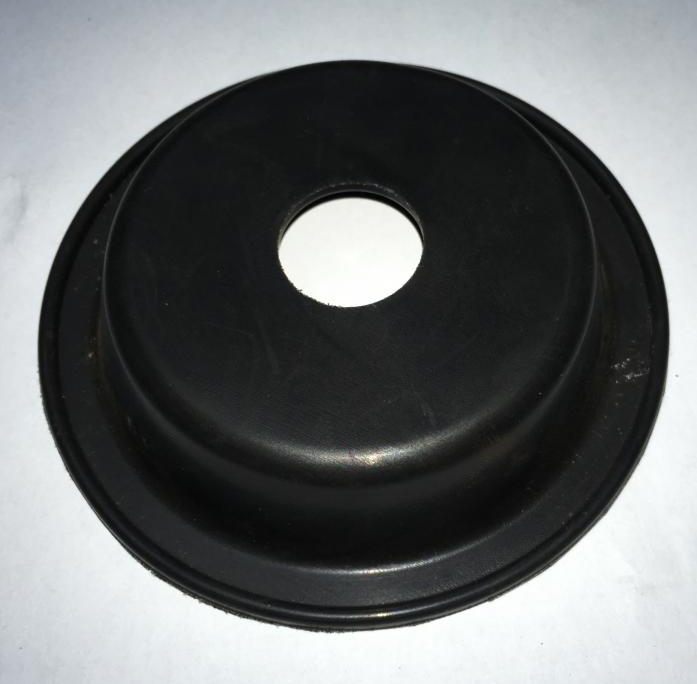
Rolling diaphragm piston servo diaphragm4
The GA series atmospheric dust removal bag filter has the advantages of stable and reliable performance, high dust removal efficiency, convenient maintenance, and long filter bag life. Widely used in industries such as building materials, ceramics, metallurgy, grain, chemical engineering, casting, etc. Compared to high-pressure reverse blowing bag dust collectors, there is more design and maintenance of supporting auxiliary equipment.
The folded bag dust collector consists of 6 points, 1 inch, 25 inch, small ash hopper, V-shaped clamp, V-shaped cloth clamp, spraying device, pulse valve diaphragm, spraying dust collector accessories, spraying system, dust collector accessories, pulse valve diaphragm, etc.
The hanging device of the folded bag dust collector is the main equipment for dust removal equipment, ash discharge, air supply, and other equipment feeding, suitable for powder and granular materials. Classification: Dischargers are mainly divided into A-type dischargers and B-type dischargers.
Produce bag type dust remover series cyclone type dust remover series Electromagnetic pulse valve series pulse controller series dust remover bag type dust remover framework series discharger series hanging device series pulse valve diaphragm series cylinder series.
PPC gas box pulse bag dust collector DMC pulse bag dust collector HMC single machine pulse dust collector MC pulse bag dust collector XMC pulse jet bag dust collector.
Daily maintenance and precautions of pulse bag dust collector equipment. The working principle of bag dust collector and the introduction to the repair and maintenance methods of bag dust collector. Precautions during debugging of bag dust collector. Precautions before stopping the operation of bag dust collector.